AIRBAG VEST BLADDER MANUFACTURING
As part of business diversification, We were involved in developing airbag vests for motorcycle riders. These motorcycle airbag vests inflate in a fraction of a second to protect the rider in the event of a crash or impact. The resulting air cushion protects the rider’s spine, ribcage, and neck/collarbone region.

Step 1 : Material Identification
The construction of most Motorcycle Air Bag Vests follows a similar pattern
- The internal bladder comprises of a 4 m long seamless polymer tube of 80 mm diameter, Layflat width of 125 mm, and 0.2mm film thickness.
- Sealed at the ends
- Embossed and holes punched in the Inflator assembly area
To find out the polymer tube material, FTIR spectroscopy was performed. The polymer was identified as Polyurethane/ TPU
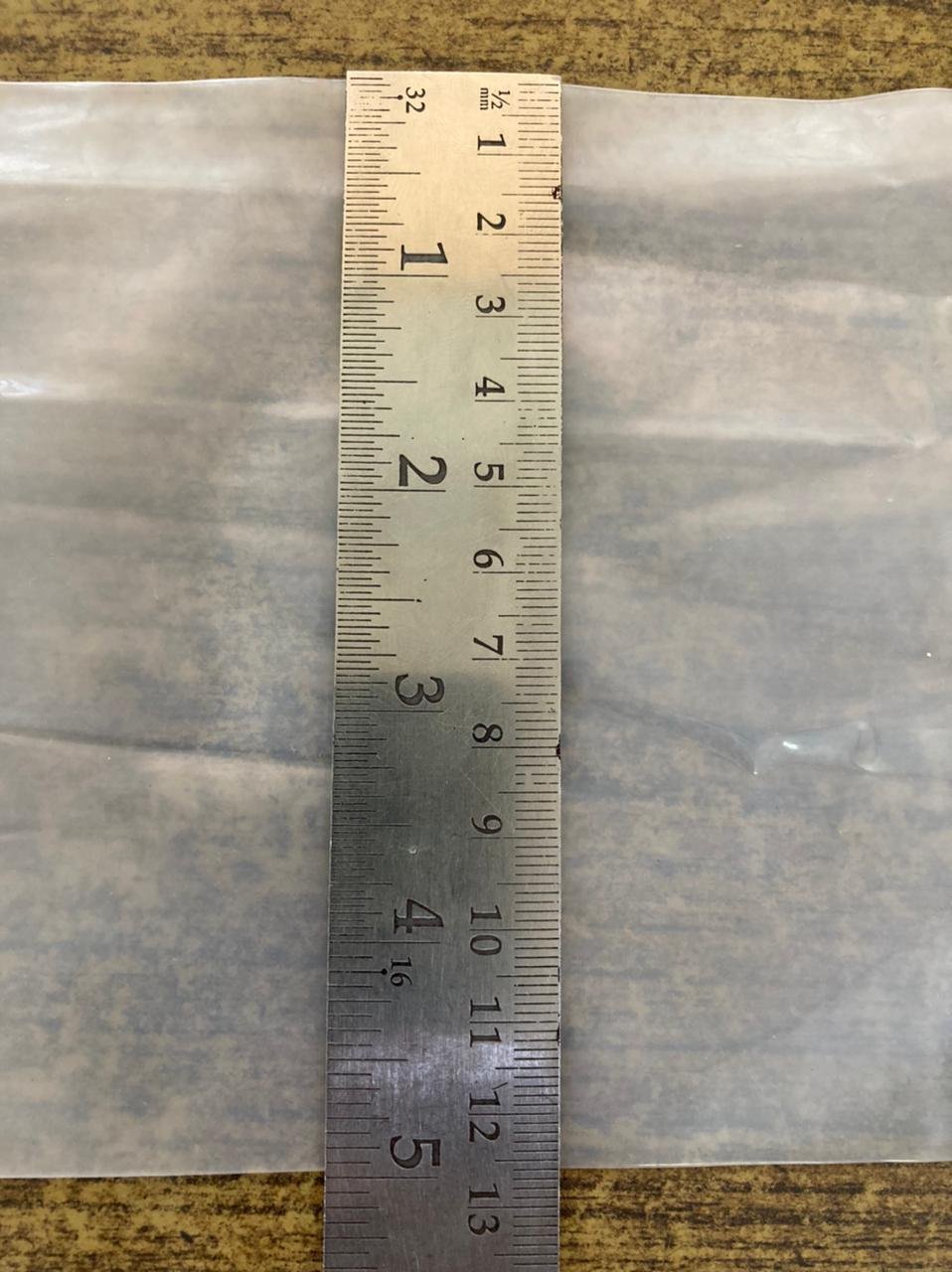



Step 2 : Mechanical / Physical Testing
Mechanical Testing for the following parameters was performed
this process helps to characterize the film material
Step 3: Sourcing
A key step in the process is to source the TPU Film
With the available mechanical properties and FTIR trace, identified a supplier in China, who had similar capabilities. Fortunately, equivalent material was available in ready stock.
100 m per roll and the pricing is per m.
Step 4 : Design & Manufacture of HF Sealing, Embossing tools
For end sealing, a top plate and a bottom sealing die were designed and machined out of brass
For embossing, a brass top plate with the emboss features was made
These sealing and embossing dies were used in a 5 kW High-Frequency sealing machine
Punches required for the process were sourced
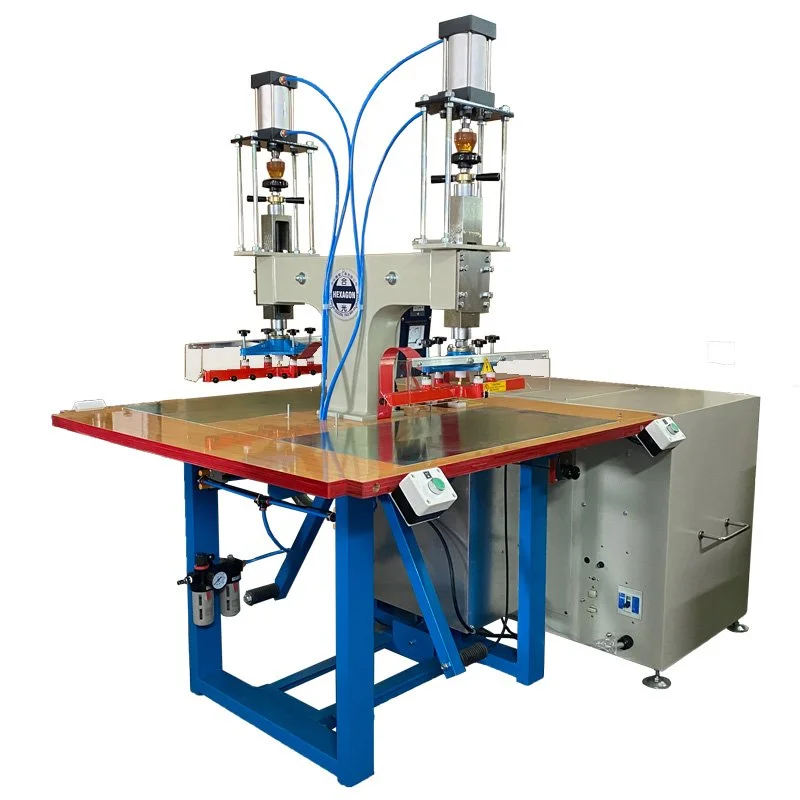
Step 5 : Pilot Production
An initial production of 25 pieces was planned for testing purposes
the production process is as follows
Tube Cutting and Marking
Insertion of silicon rubber pad into the tube - (used for embossing)
Insertion of HDPP cutting pad into the tube - (used for hole punching)
Insertion of inflator backplate into the tube
Embossing
Removal of silicon rubber pad from the tube - (used for embossing)
Hole punching
Removal of HDPP cutting pad from the tube - (used for hole punching)
Blowoff to remove any dust/debris
HF Sealing of ends
Inflator Assembly
ReSULTS
IMPROVED PRODUCT PERFORMANCE & QUALITY