DESIGN AND MANUFACTURE OF AIR SEAT CUSHION TOOLINGS
At Rajans Automotive, the majority of my work involved design and manufacture of cellular air seat cushion molds, dies, and templates for every stage in the process. Thermoplastic polyurethane (TPU) is the most commonly used material for air seat cushion manufacturing. The use of PVC is also possible in certain cases. The process of manufacturing cellular air seat cushions/seat pads is as follows
Raw material inspection
Thermoforming of the shell - Top Layer
Blanking of the shell - (Cutting Stage 1)
Hole punching on the shell for valve fittings
HF welding of the valve fitting on the shell - (HF Welding 1)
Blanking of the bottom layer - (Cutting Stage 2)
HF welding of the shell & bottom layer - (HF Welding 2)
Flash Trimming - (Cutting Stage 3)
Testing
Packing & Dispatch
Motorcycle
Air Seat Cushion
Lumbar Support / Air Backrest
THERMOFORMING MOLDS
In Cellular air seat cushion manufacturing, cavity molds with zero or minimal draft are used for the thermoforming of shells. Matching plugs are used in conjunction with the cavity molds to aid in uniform material distribution. Shown below are some of the thermoforming molds I made.
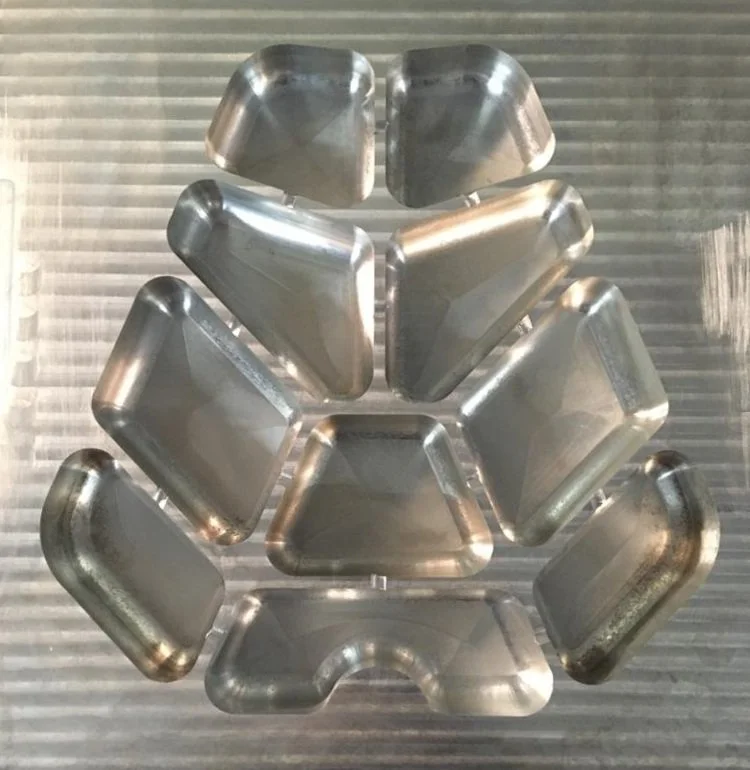
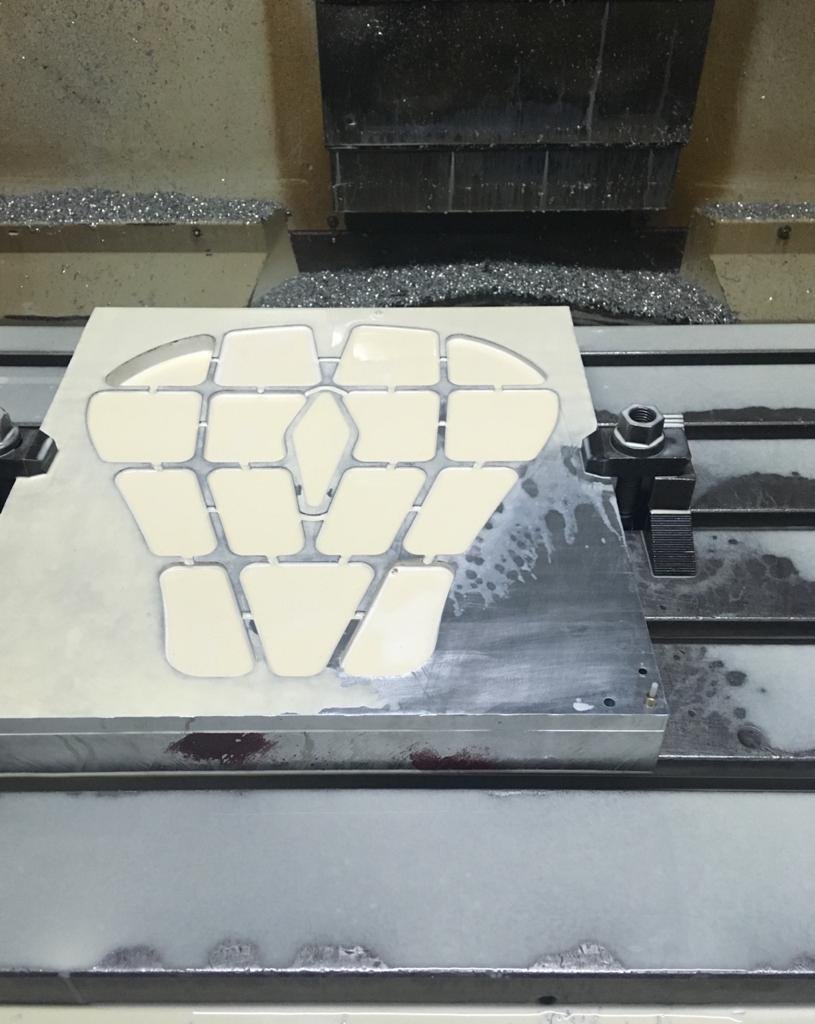
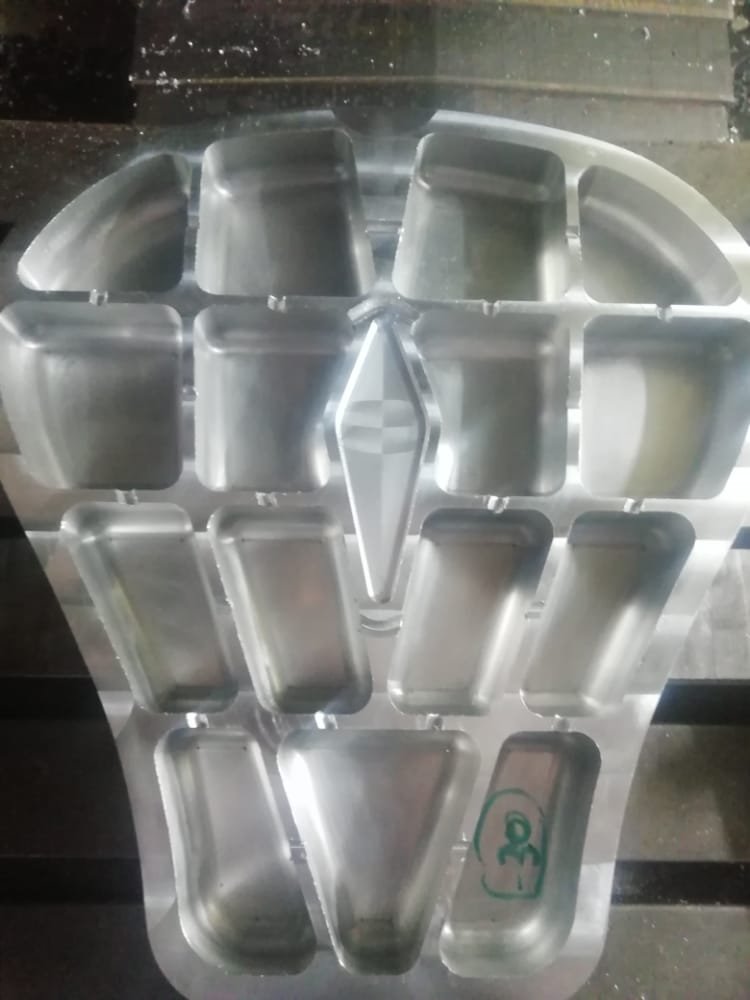

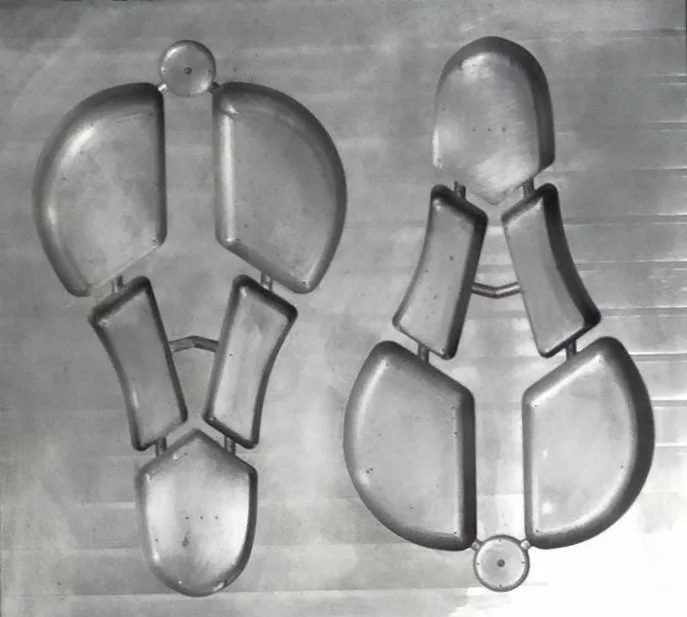
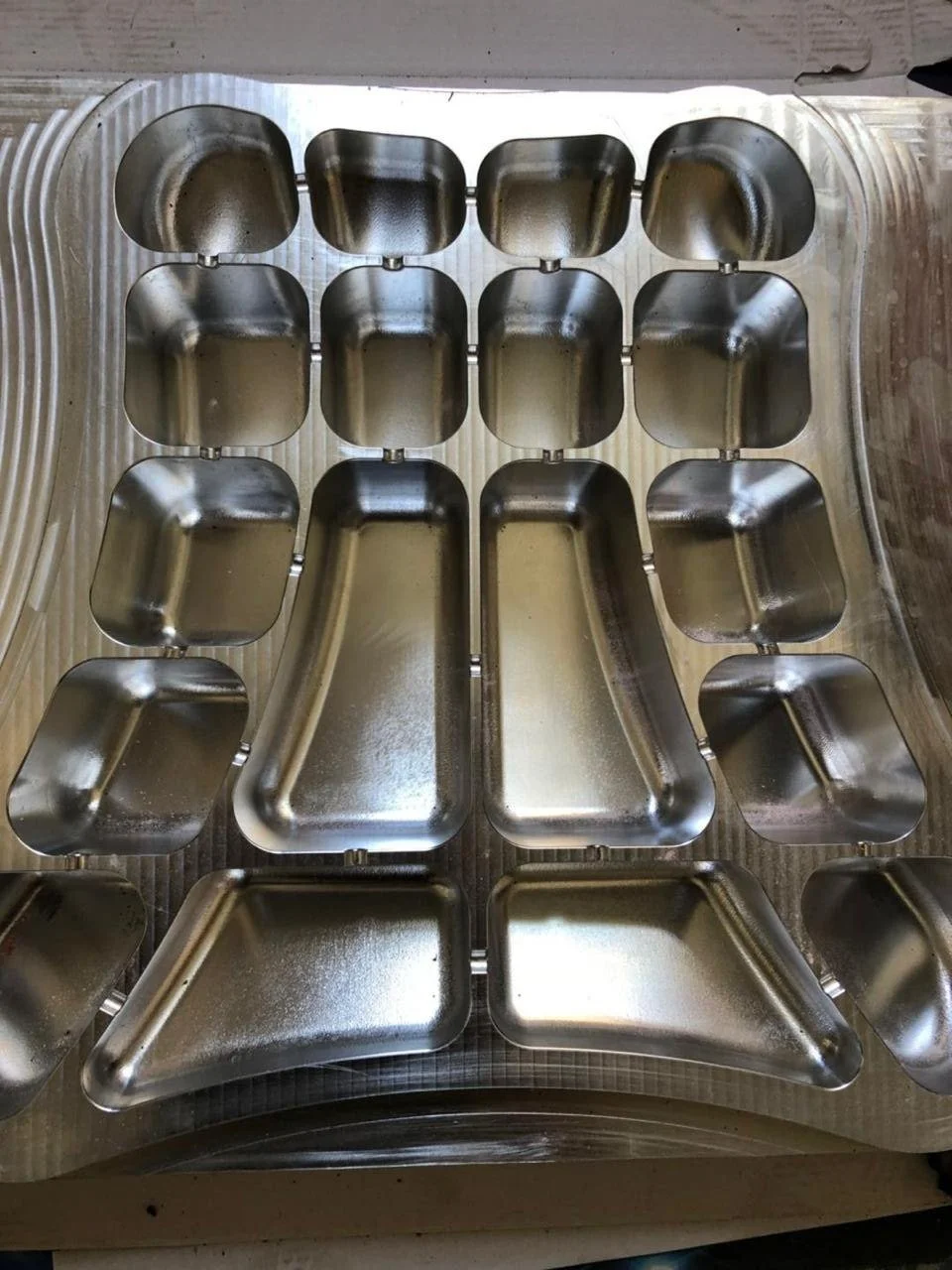
THERMOFORMING PLUGs
In Thin-gauge thermoforming operation, plugs are typically manufactured using subtractive manufacturing techniques - I adopted a method combining 3D printing, resin casting technique, and glass microspheres to produce near-net shape syntactic foam plugs - This method helped us save about 65% in costs
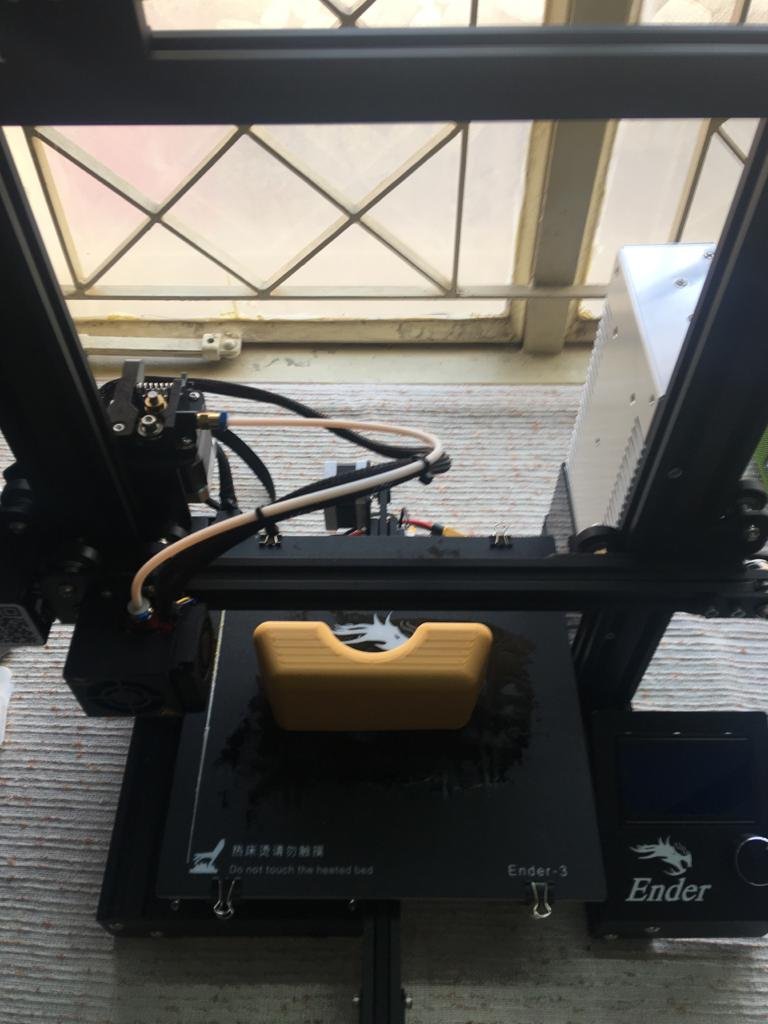
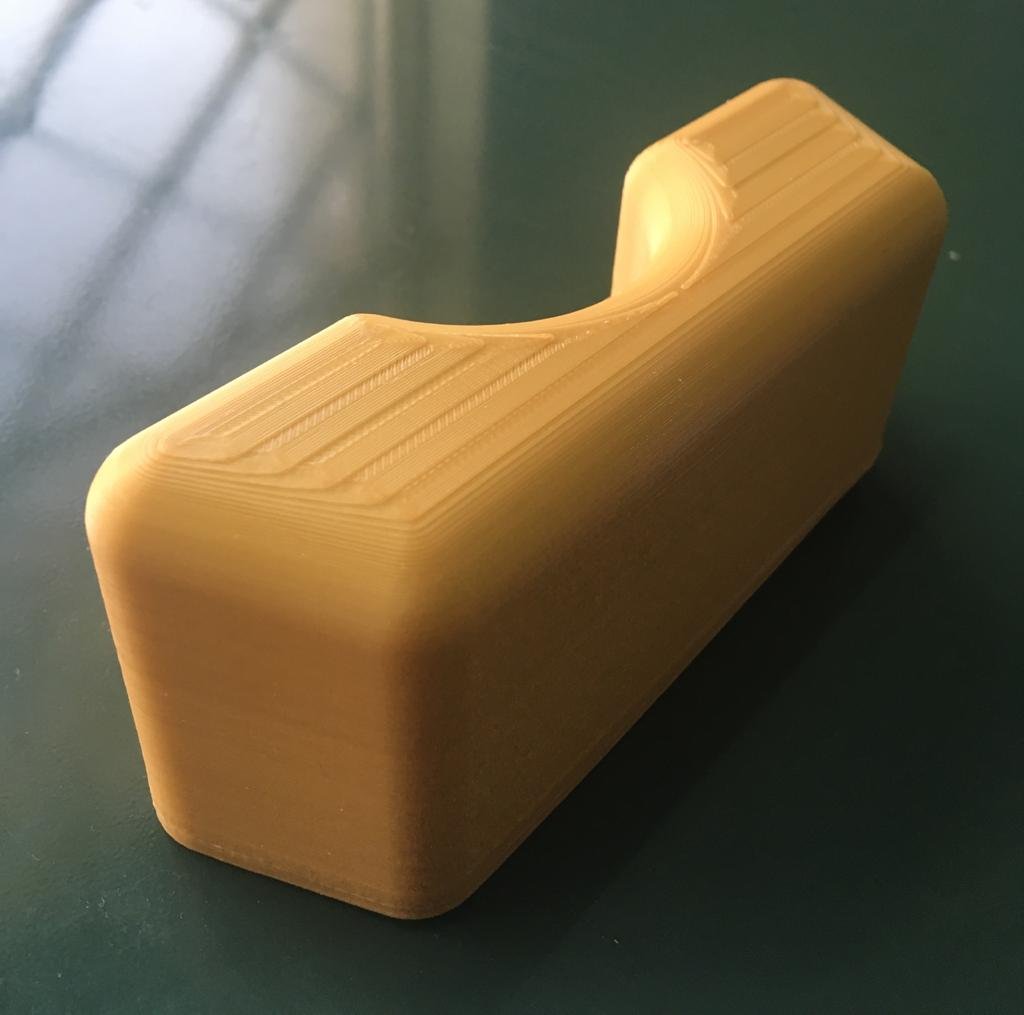

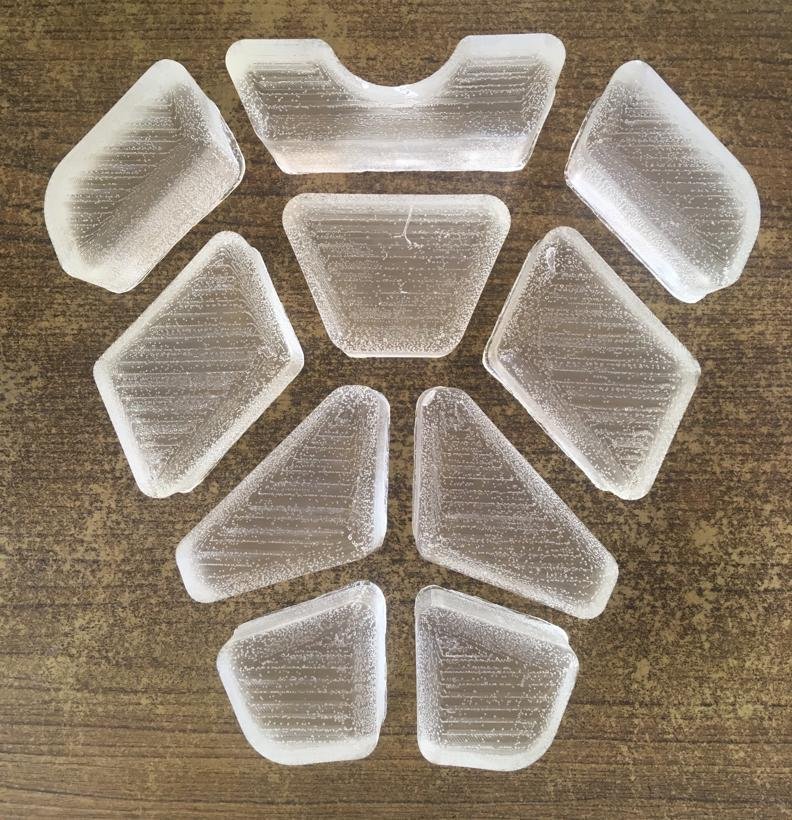
HF Welding / Sealing Dies
Also known as radio frequency welding, this process uses electromagnetic energy and pressure to permanently fuse polar thermoplastics together. Shown below are some of the sealing dies that I designed for processes - HF Welding 1 & HF Welding 2.
HF Welding 1 uses a 5 kW machine
HF Welding 2 uses a 15 kW machine
For low-volume production / Pilot production, Conceived Hybrid tooling concept - a combination of thermoforming mold and sealing die - decreased tooling cost by 50%
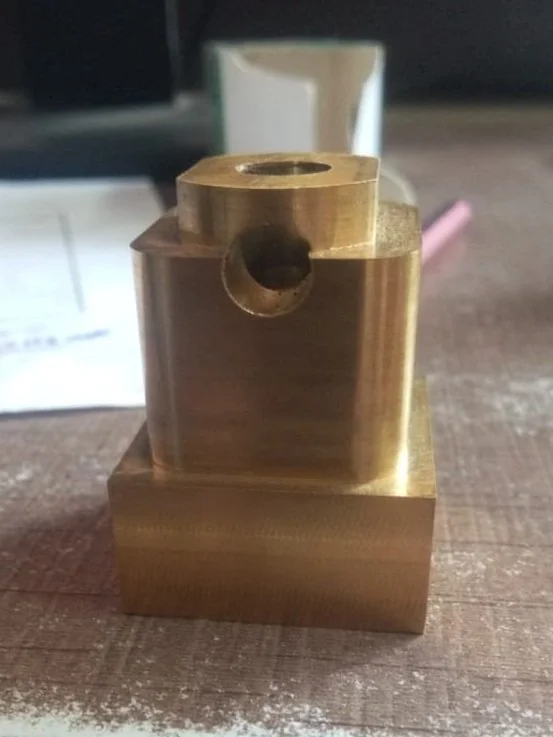
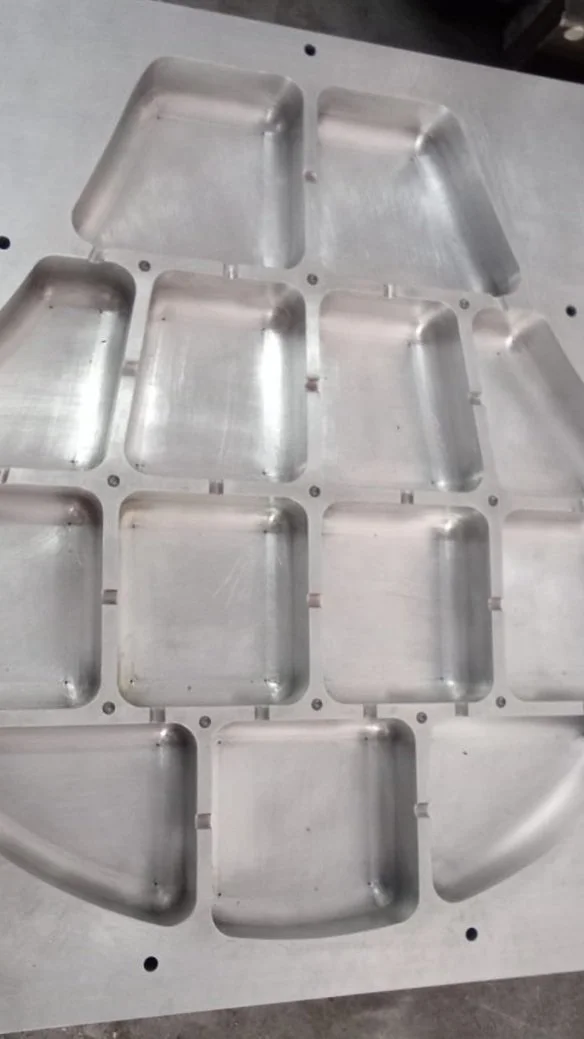
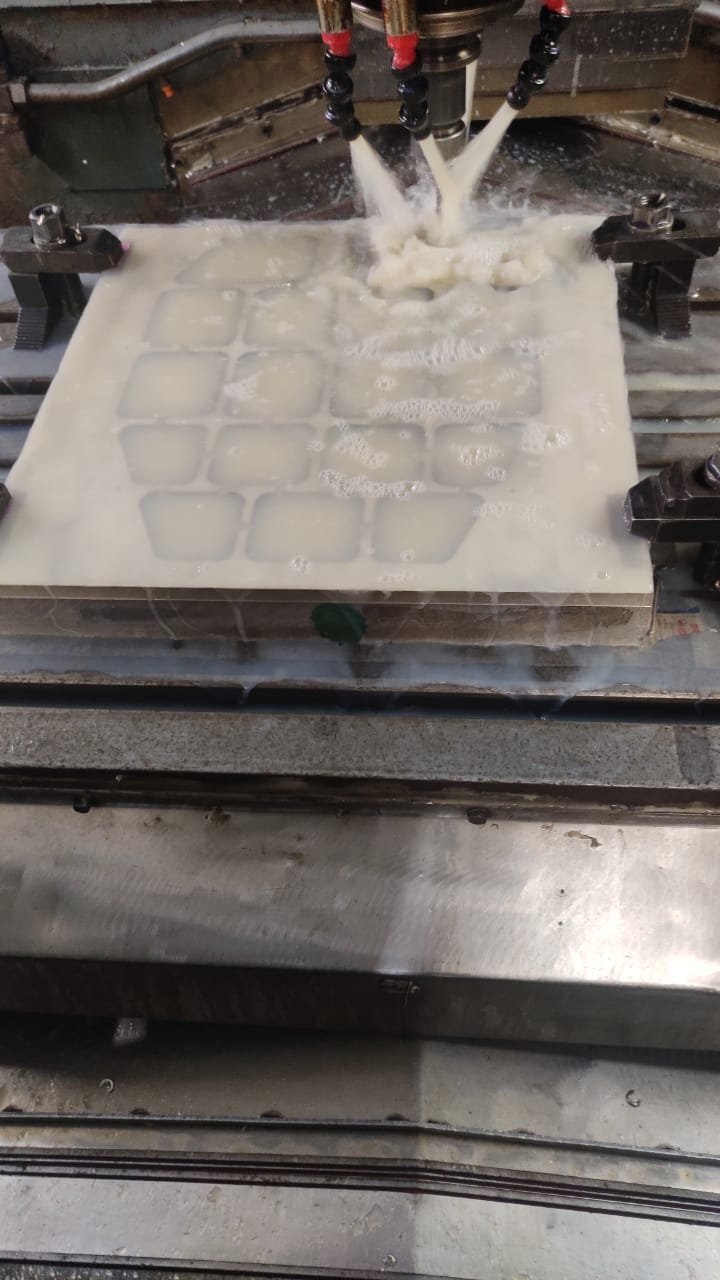
CUTTING DIES
Cutting Dies are required for
Blanking of the shell - (Cutting Stage 1)
Blanking of the bottom layer - (Cutting Stage 2)
Flash Trimming - (Cutting Stage 3)
All these operations are carried out on a 40-ton hydraulic press with limit and depth settings.
Stage 1 & 3 dies are constructed using steel rule dies & Russian birch plywood. Stage 2 dies are constructed using heavy gauge steel rule dies and welded supports.
Following are some of the cutting dies I designed.
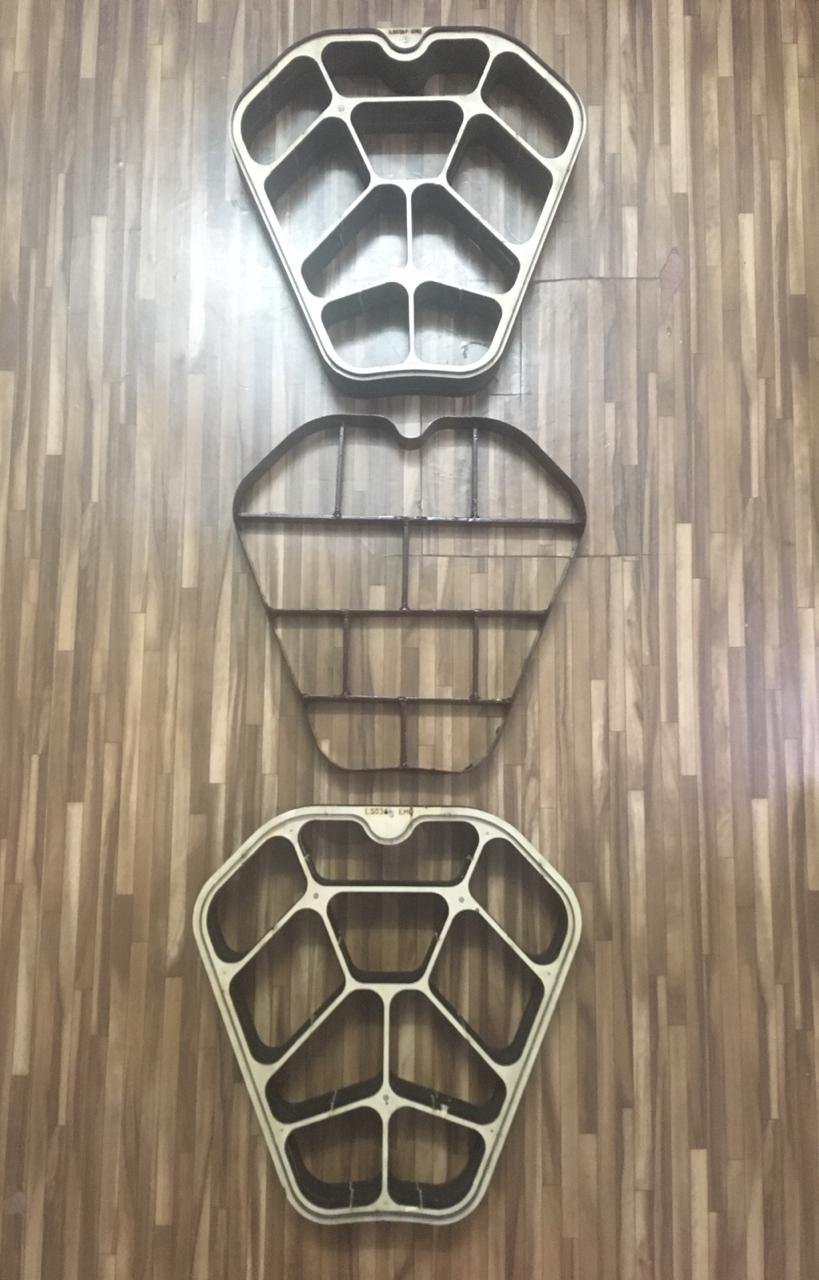
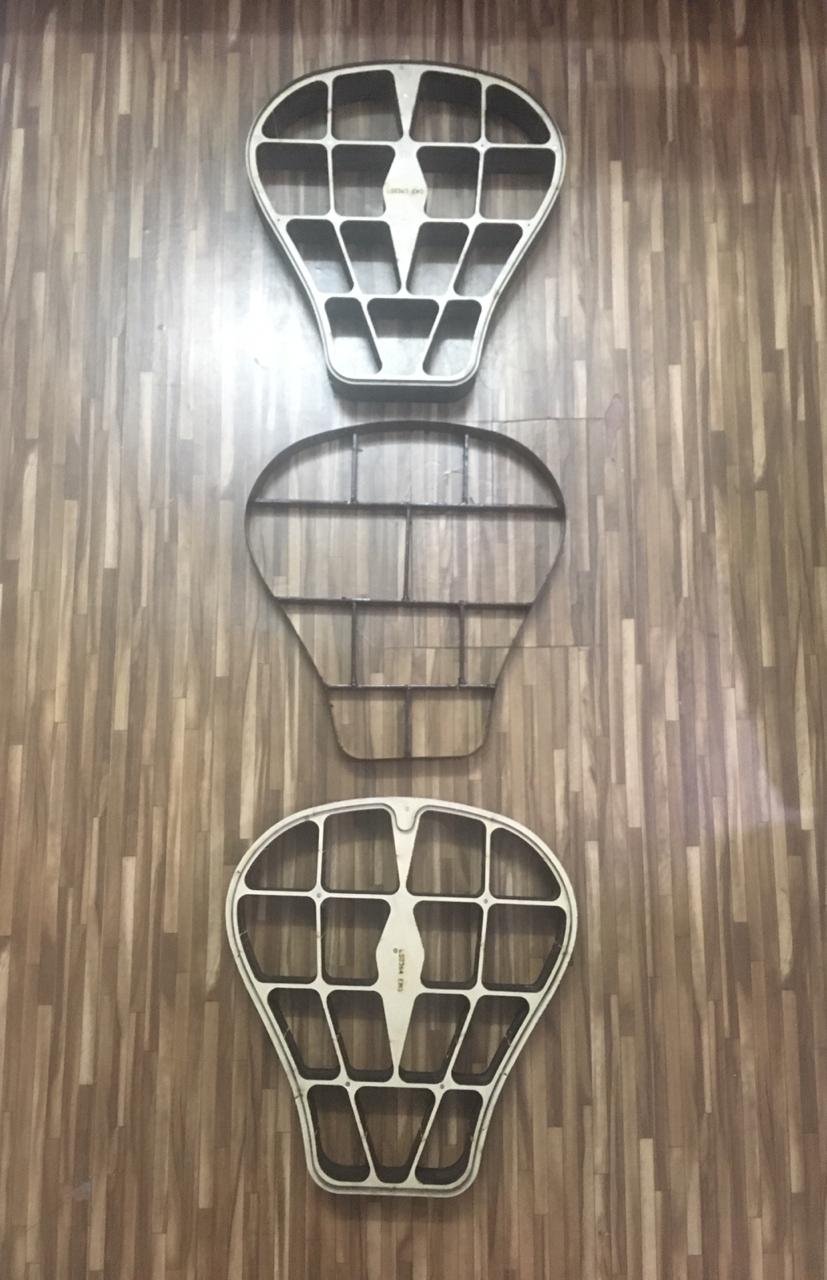
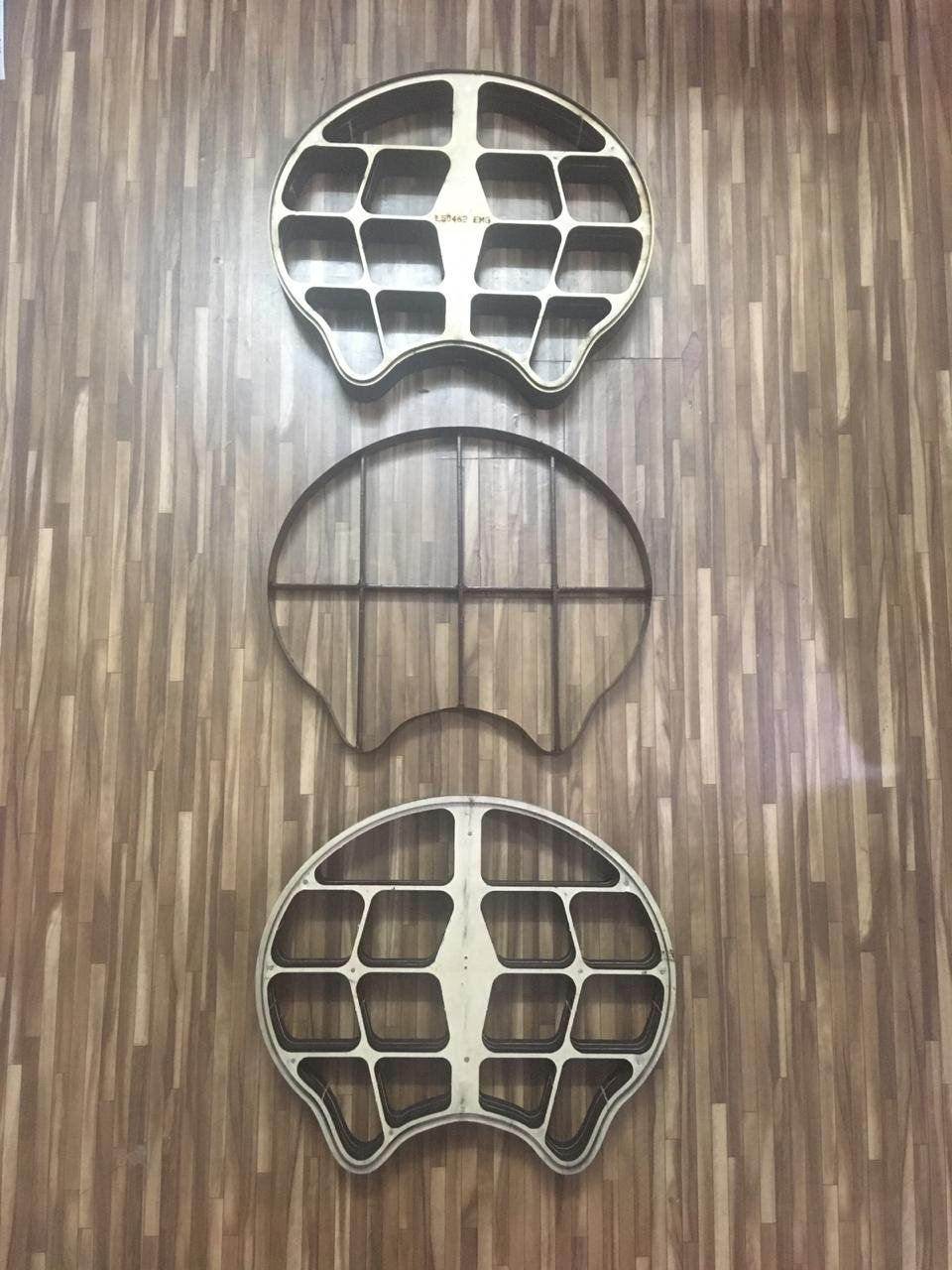
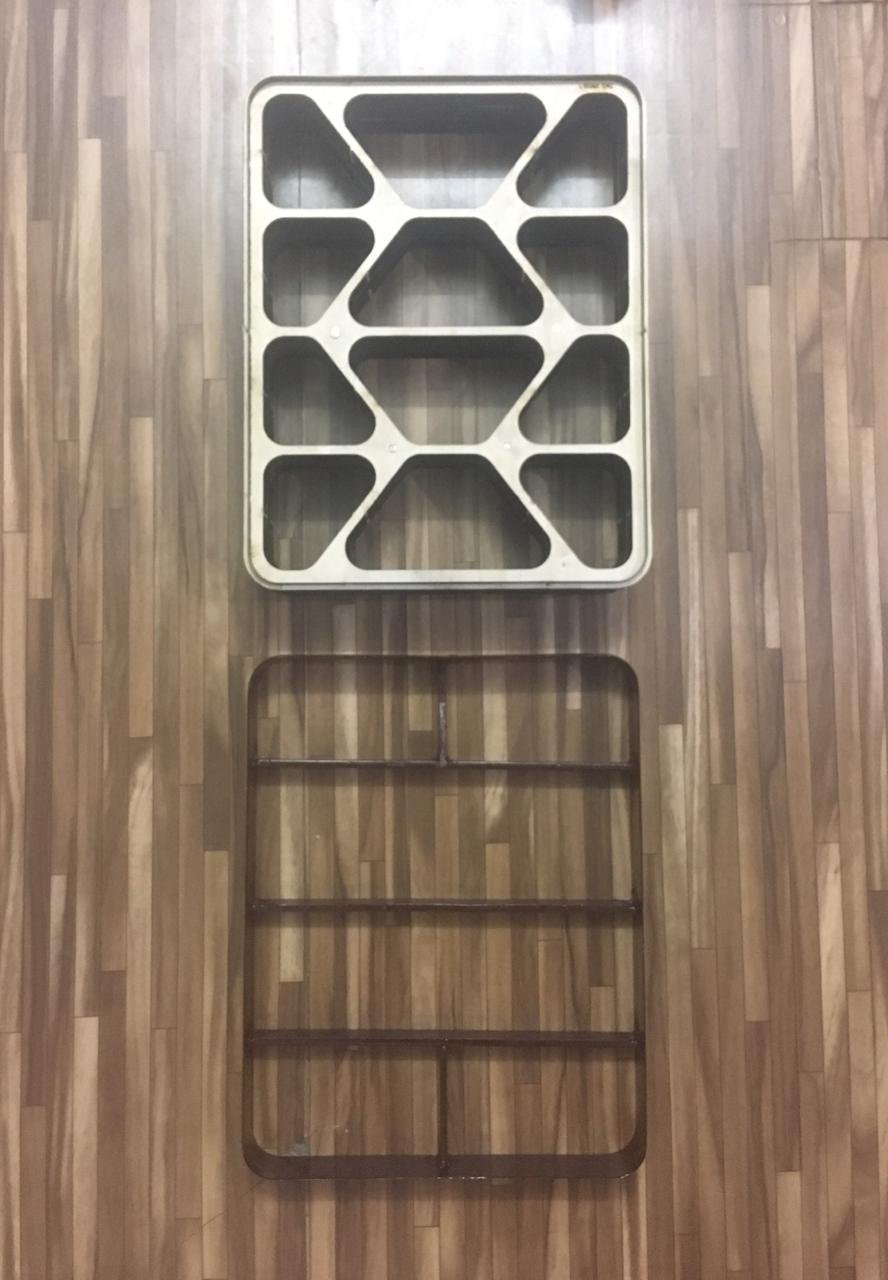
RESULTS
> Adopted 3D printing and resin casting for the production of syntactic foam plugs - minimized plug cost by 65%
> Conceived Hybrid tooling a combination of thermoforming mold and sealing die - decreased tooling cost by 50%