SETTING UP AIR SEAT CUSHION MANUFACTURING PLANT
BACKGROUND
Rajans Automotive introduced the Ride-on-Air series of air cushions in 2015. This was a time when gel seat pads were the only comfort option available for motorcycle seats in India. The company controlled the design aspects of the product, cushion cover production in India & the air cushion manufacturing was realized using a Chinese partner. Demand for the product grew progressively and to reach more users there was a continued drive to lower the cost of the product. In 2019, we decided to set up India’s first-of-its-kind Air Seat Cushion Manufacturing Plant in Coimbatore, Tamilnadu.
Key Challenges :
Finding the right TPU material and supplier
Identifying the correct machinery and its manufacturers
1. Finding the right TPU material and supplier
The manufacture of air seat cushions is predominant in Dongguan city in central Guangdong Province, China. There are very few manufacturers outside of China. I focused on TPU Film Suppliers in and around the Guangdong Province & identified around 18 suppliers who supply relevant raw materials. The following steps were carried out on repeat mode until we found the right supplier.
> Check for previous experience in supplying for a similar product
> Request for Datasheets, Test Reports
> Purchase of Film Samples
> Ship them to India
> Testing of Film Samples
> Comparison of test results
Finalized two reliable suppliers for long-term material supply
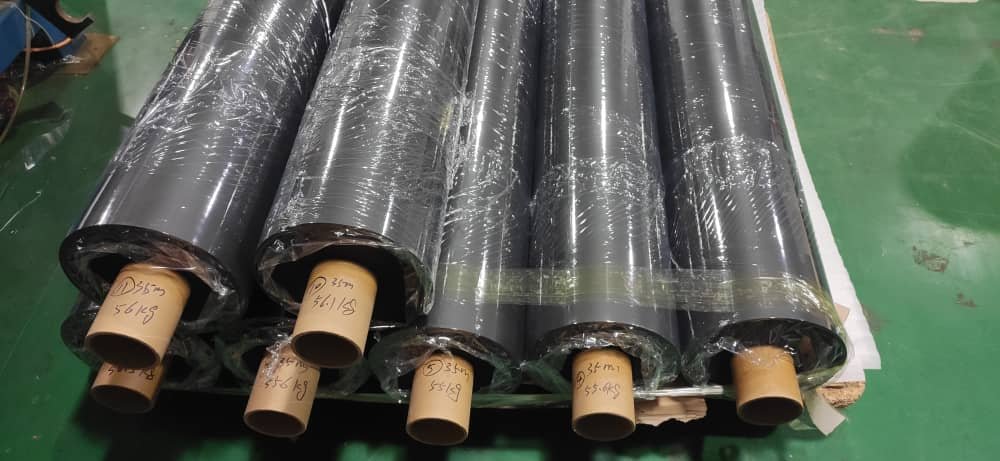
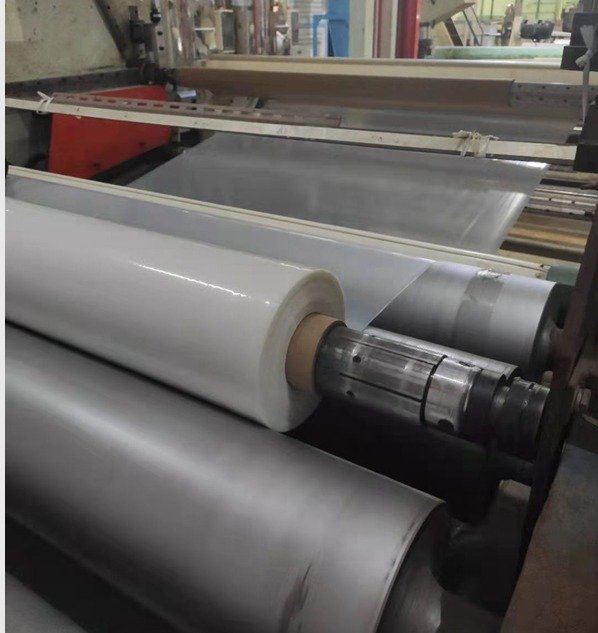
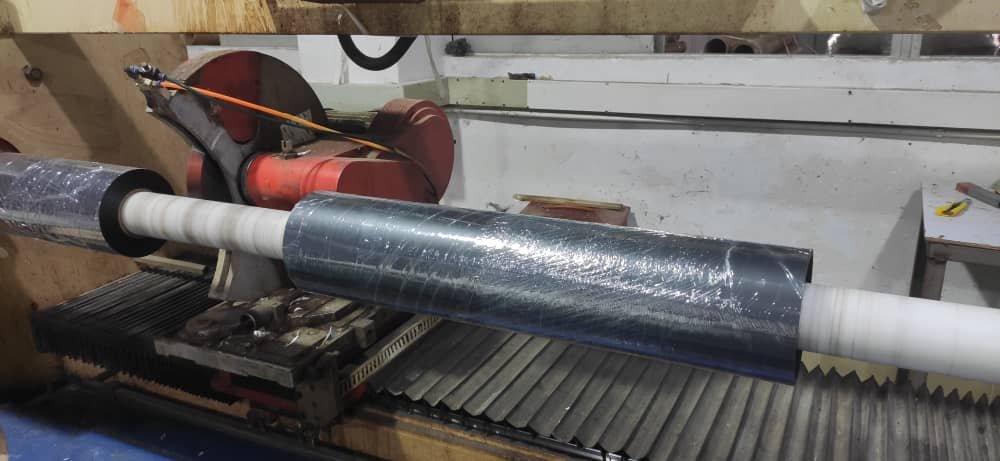
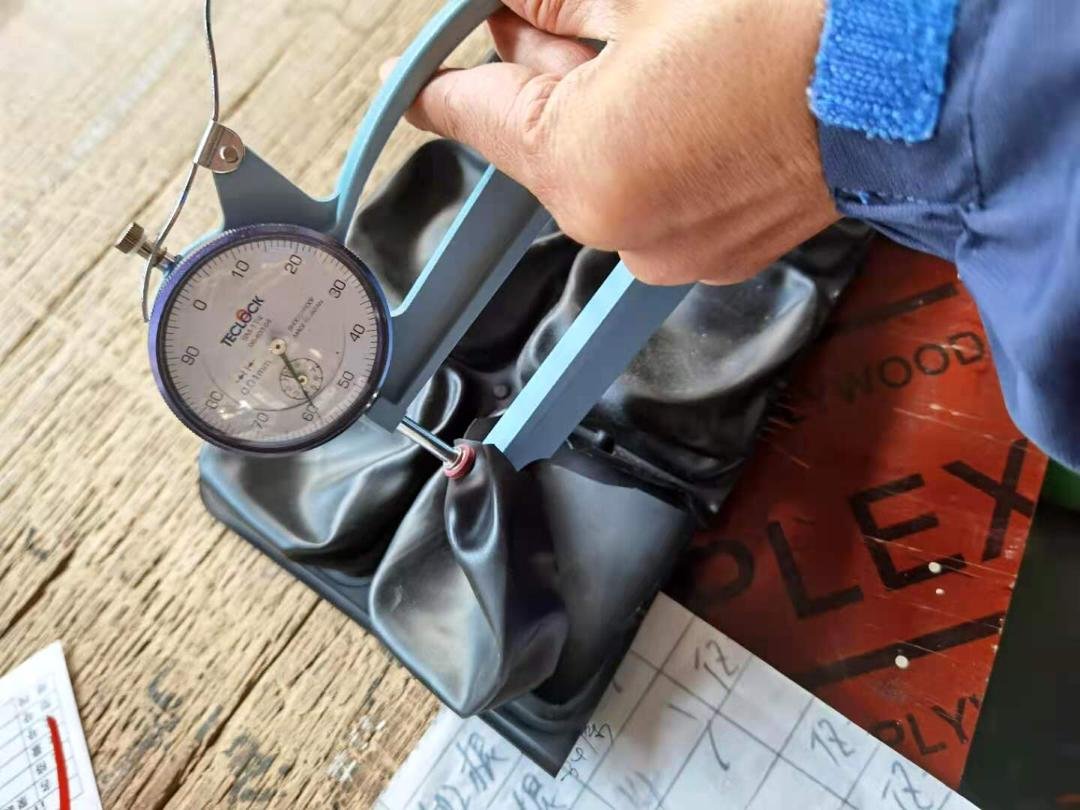
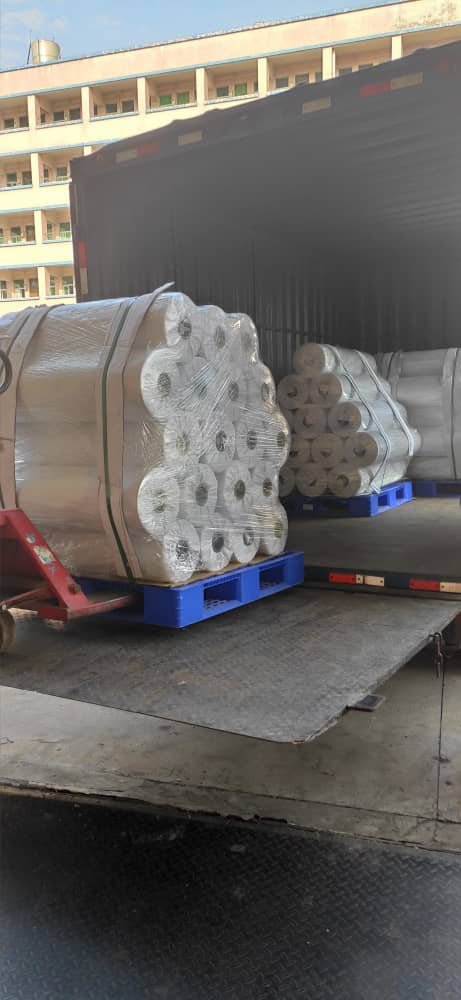
2. Identifying the correct machinery and its manufacturers
Based on the product features and the feature creation sequence, the manufacturing process, required tooling, and required machinery were decoded. Following machines are required for manufacturing air seat cushions.
> Thermoforming Machine
> HF - High Frequency Welding Machine - 5 Kw
> Hydraulic Cutting Press - 40 Ton
> HF - High Frequency Welding Machine - 15 Kw
> Air Compressor, Pneumatic lines etc.
A minimum of 3 suppliers was considered for every machinery. Decisions were taken based on the Pugh matrix considering machinery performance, features, cost, delivery timeline, service/spares support, etc.
THE SET-UP
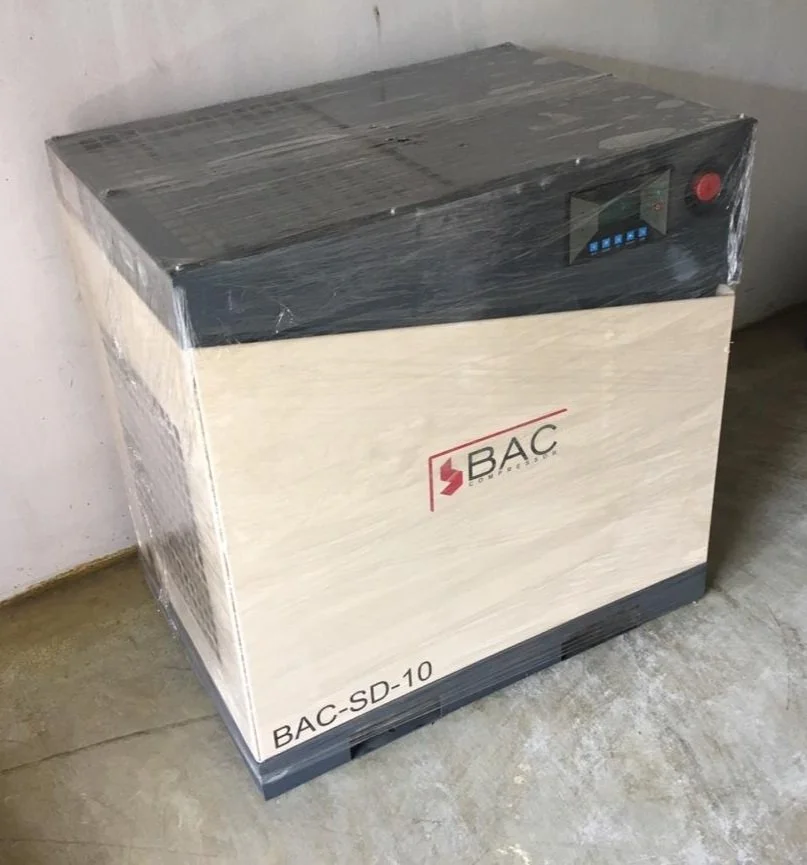
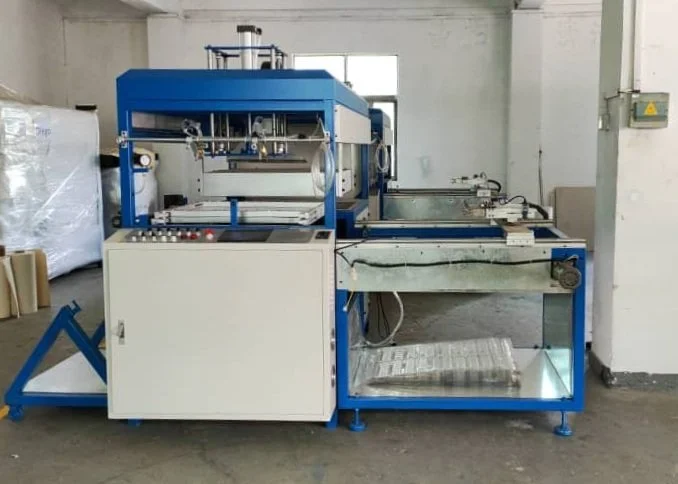
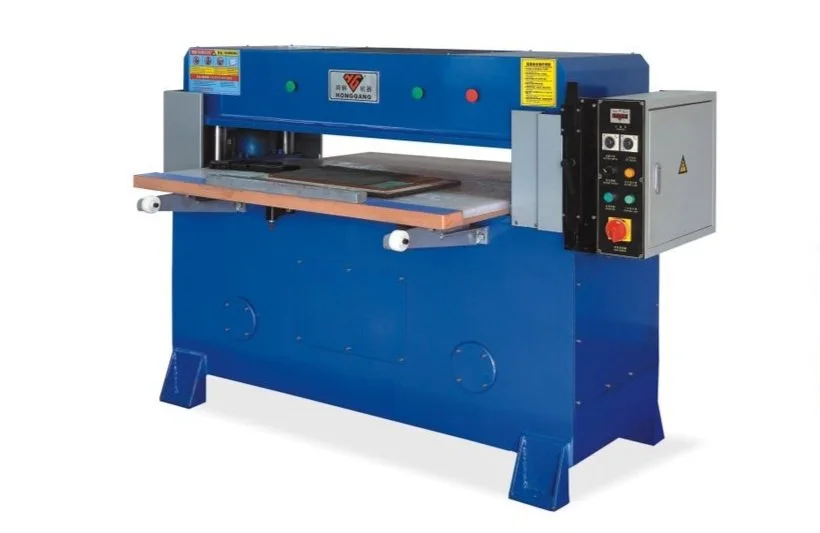



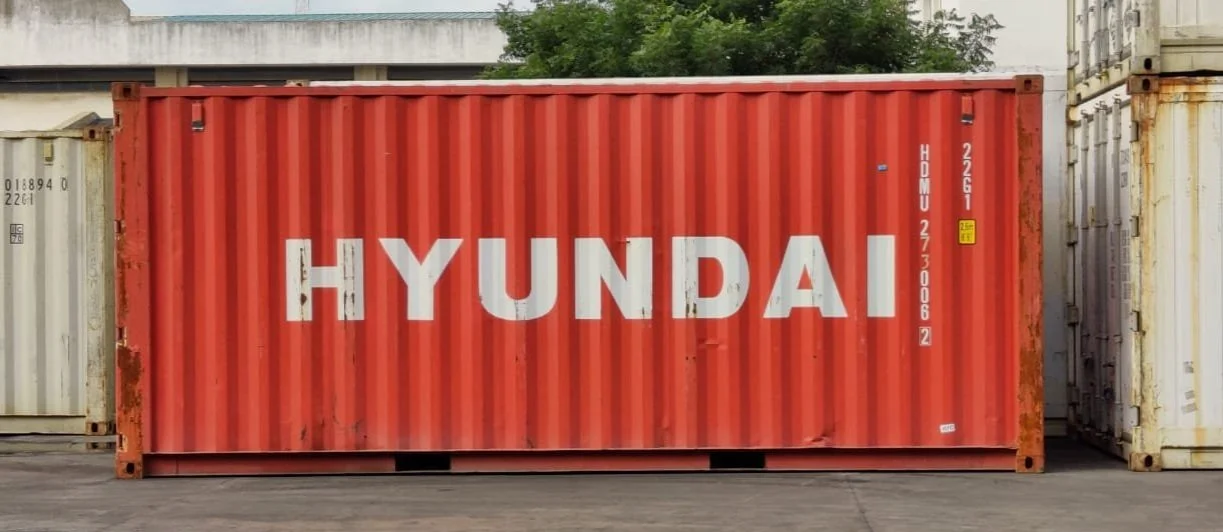
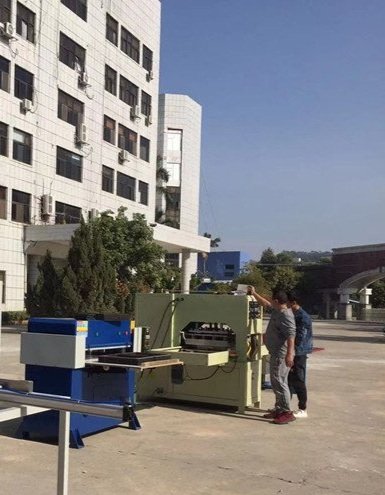
Results
Reduction in finished product cost by 70% and minimized the company’s dependence on imports