CusTOM AIR SEAT FOR HD FATBOY
with Inbuilt Air Seat Cushions & PumpS
BACKGROUND
A rider friend of mine, a laparoscopic surgeon wanted to integrate our air seat cushions into his Harley Davidson Fatboy‘s - signature seat. The signature seat is an optional accessory seat offered by Harley Davidson. Following were his requirements for the project.
USER REQUIREMENTS
Separate Rider & Pillion air seat cushions for enhanced comfort
In-built air pumps for the rider & pillion air seat cushions
Unparalleled aesthetics/looks (logo hot foiling, pop rivets, etc)
The rider backrest and tour pack pillion backrest are to be finished in line with the seat design
HD Signature Seat with Rider Backrest
HD Tourpack Backrest
Step 1 : Pump Housing Design & 3D Printing
To serve as an enclosure and shield the bulb pump from any unintentional pump squeezes / external forces
Also to safely constrain the pump valve in place
It was quickly realized using FDM 3D printing
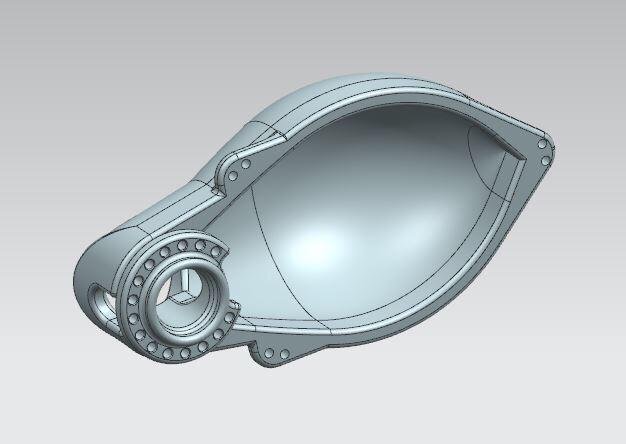
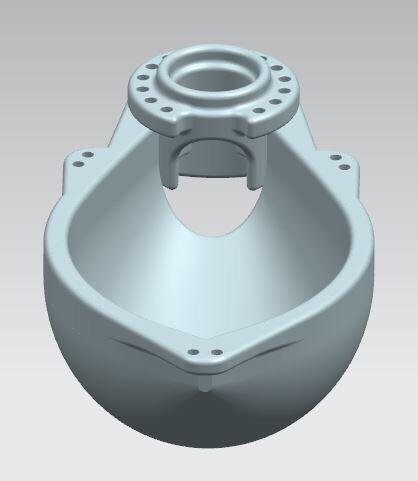
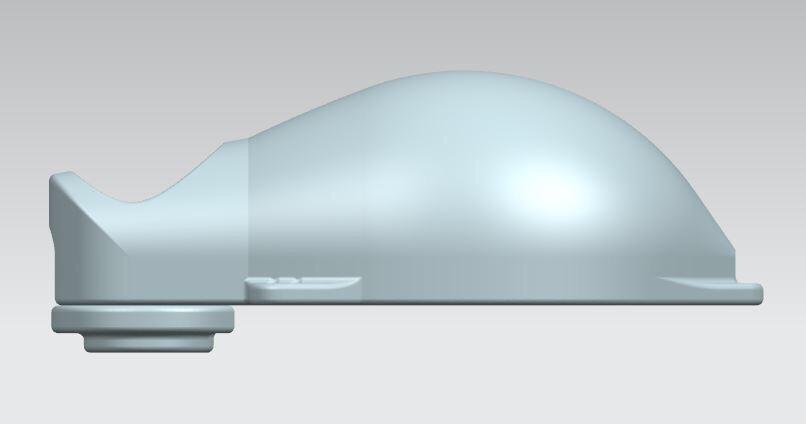
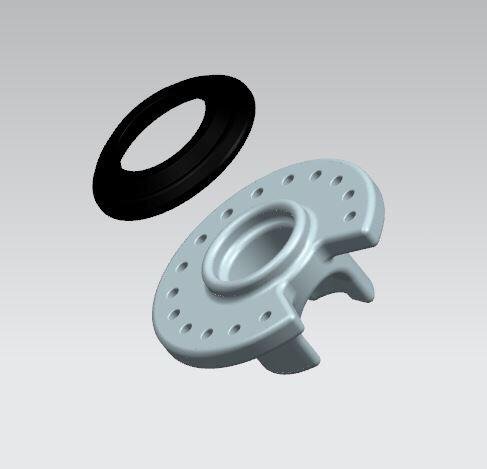
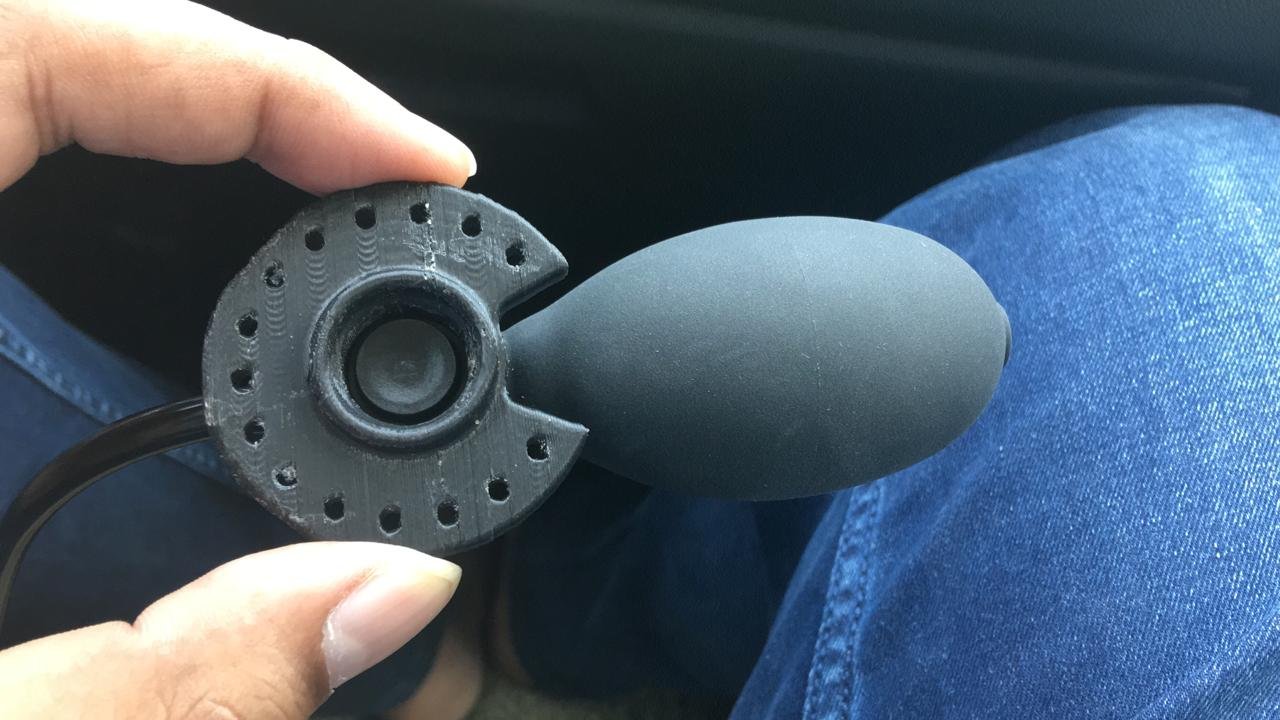
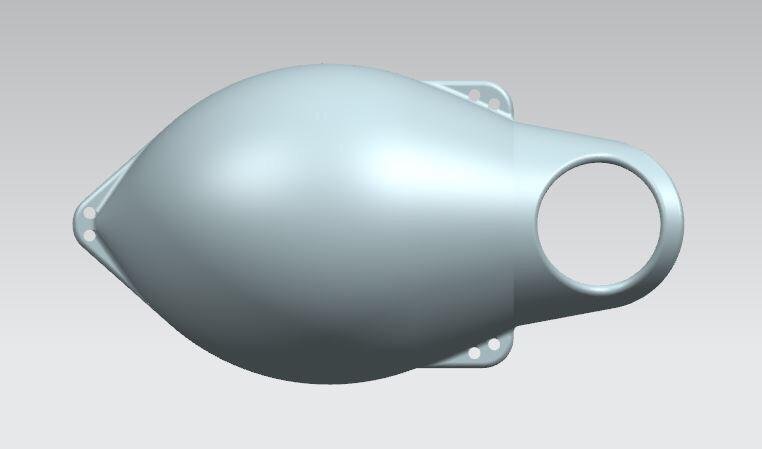
Step 2 : Air Cushion Integration & Foam Work
Based on the user requirement, seat shape & foam area available it was decided to use a cruiser cushion for the rider region and a pillion cushion for the pillion region
Seat foam was cut & trimmed by 1 inch to install air seat cushions for the rider & pillion
Two pockets were cut on the foam sides to install the pump housings
The air pumps were connected to the air seat cushions using polyurethane tubing
A softer 0.5-inch 40-density foam sheet was added on top covering the air seat cushions
Over the soft foam sheet, a 0.5 mm TPU fabric laminate was added to prevent water entry through the quilting
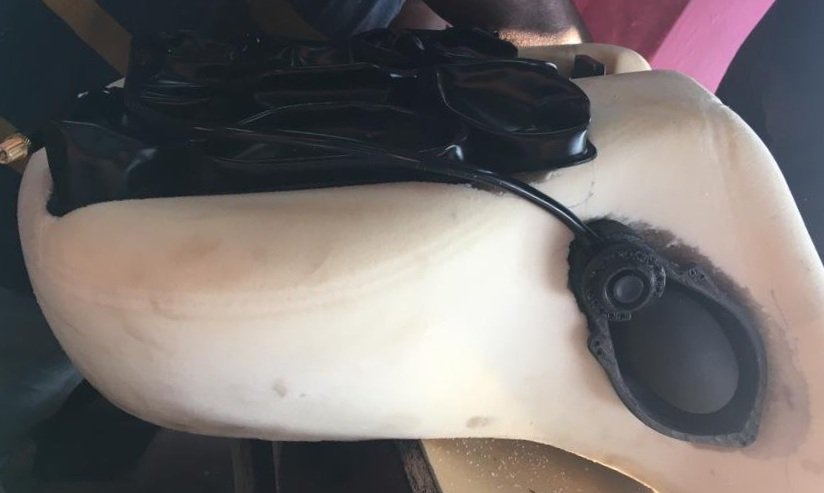
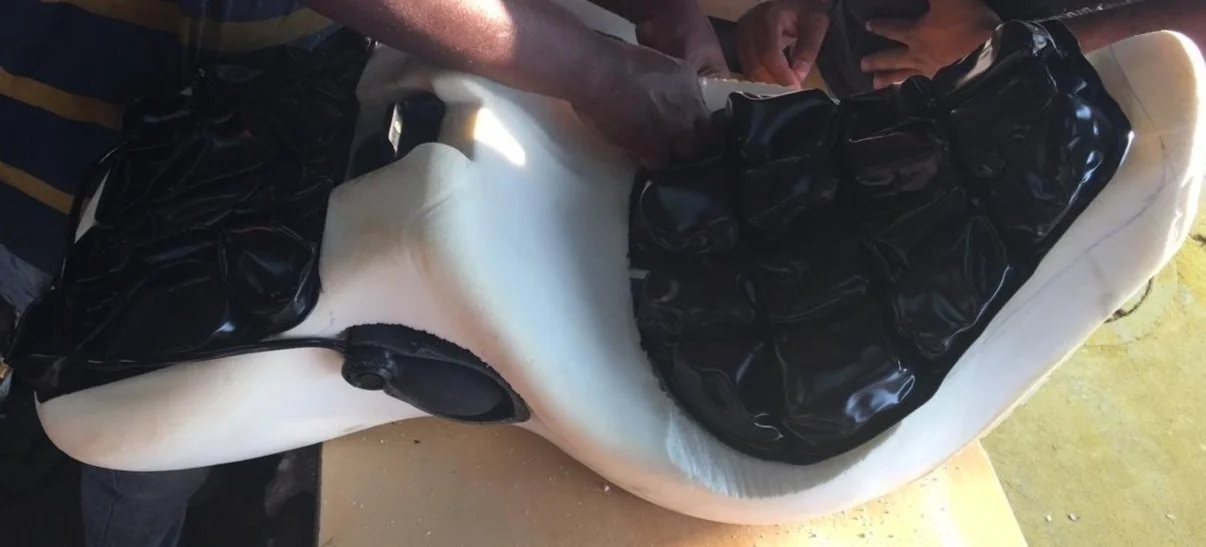
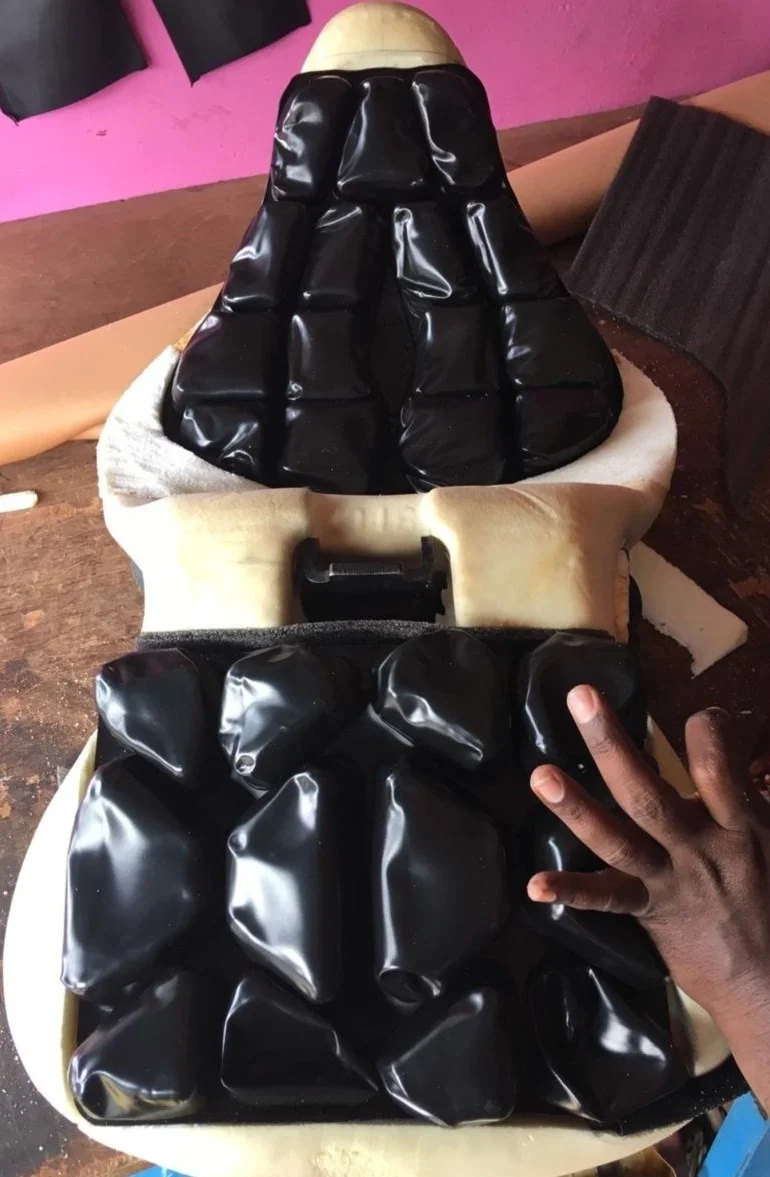
Step 3 : Hot Foil Stamping
A brass stamping/embossing die was made based on the Harley Davidson skull theme
Hot stamping was done on the rider backrest and tourpack backrest using a silver foil and hot stamping machine
Foiled regions were sprayed with 2 layers of flexible polyurethane clearcoat for durability

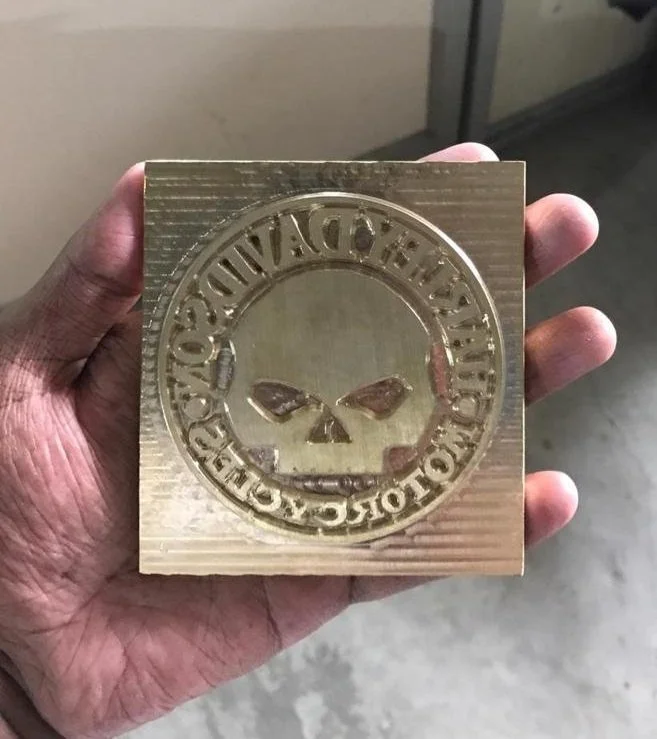

Step 4 : Seat Cover Work
The design of the seat cover was executed in line with the initial user expectations and was improvised through discussions with the user from time to time
A diamond quilting pattern was adopted for the seat cover, rider backrest, and tourpack pillion backrest
Sewing was done using black vinyl and a silver shade thread
HF Welder was used to emboss and mark the pump valve region and pump squeeze region
Silver color - Double cap rivets were added on the seat side leaflets, rider backrest, and tourpack pillion backrest for aesthetics
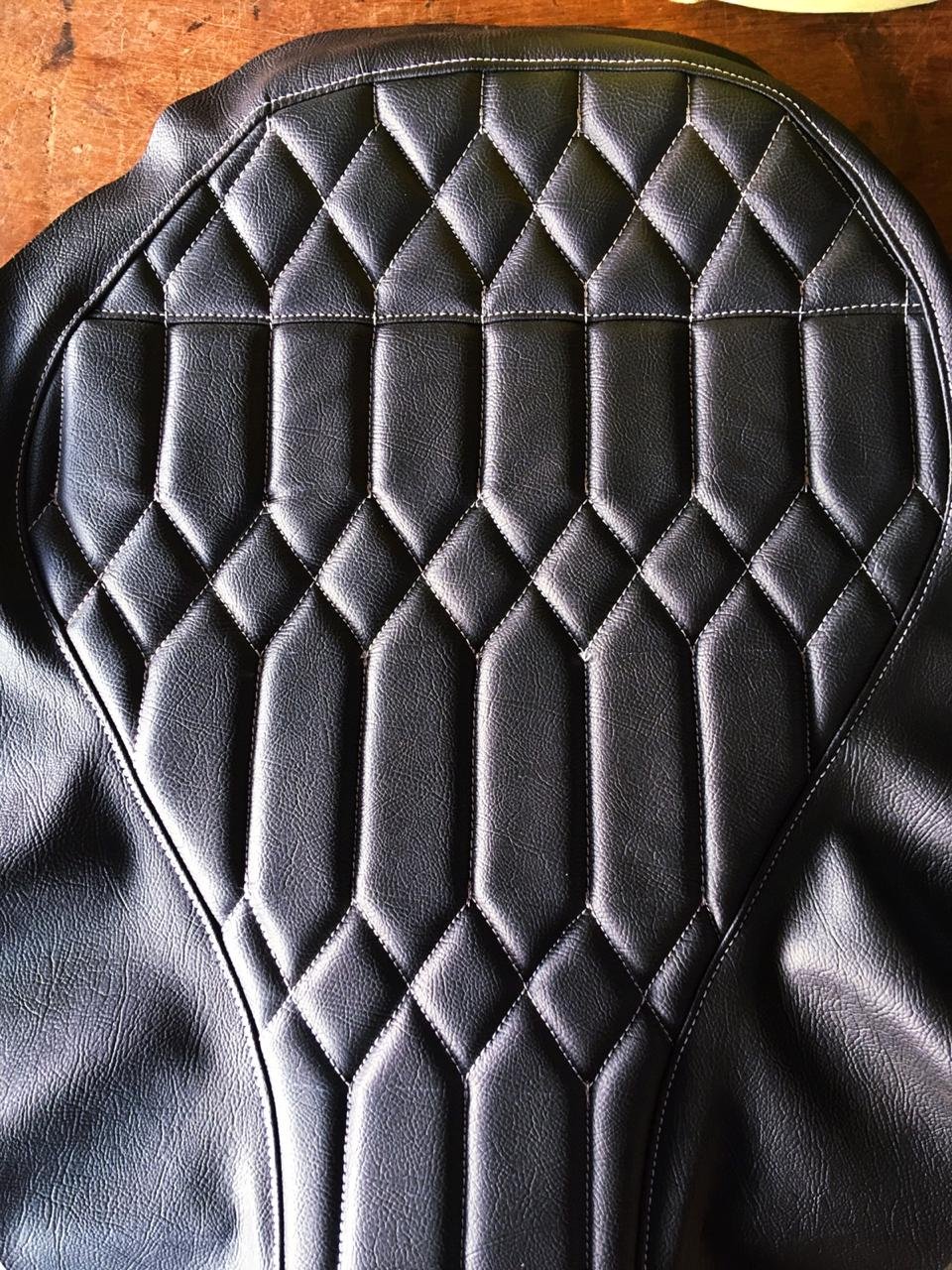
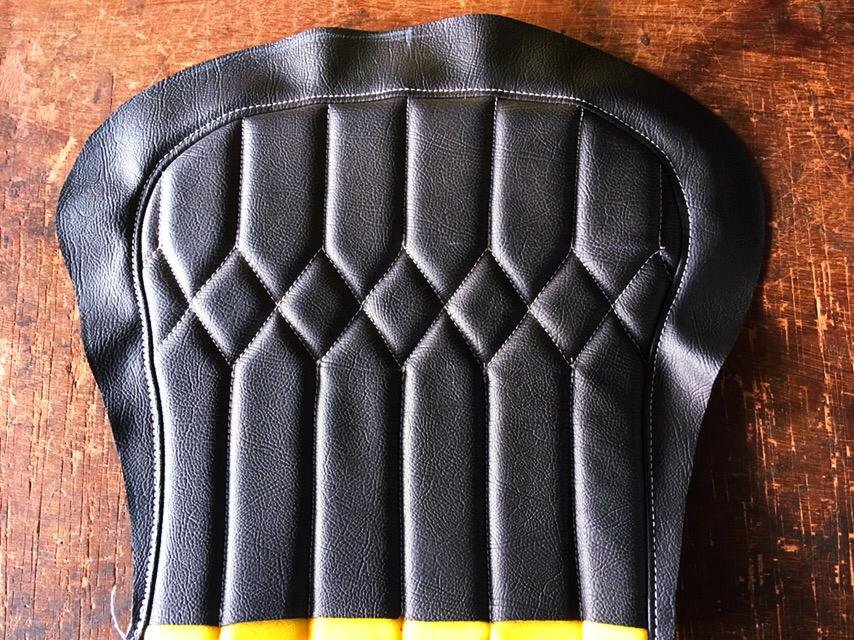
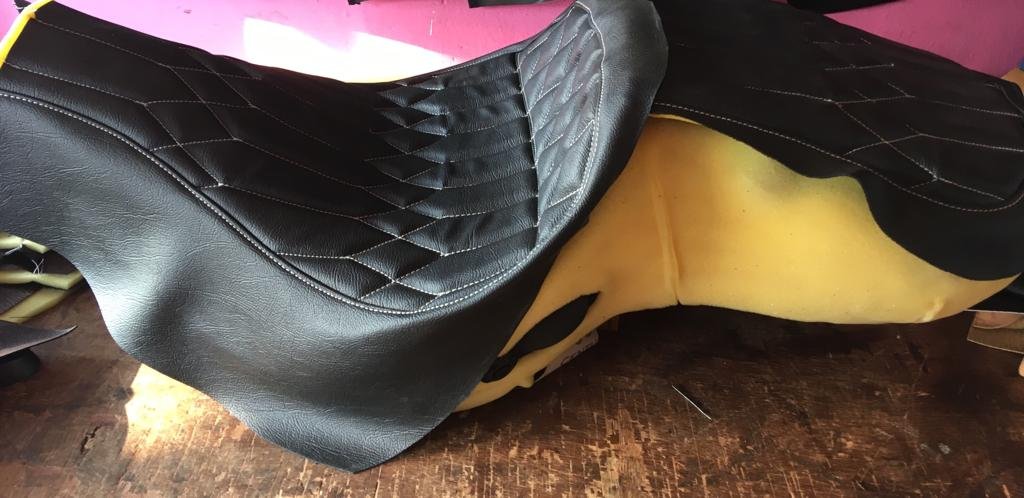
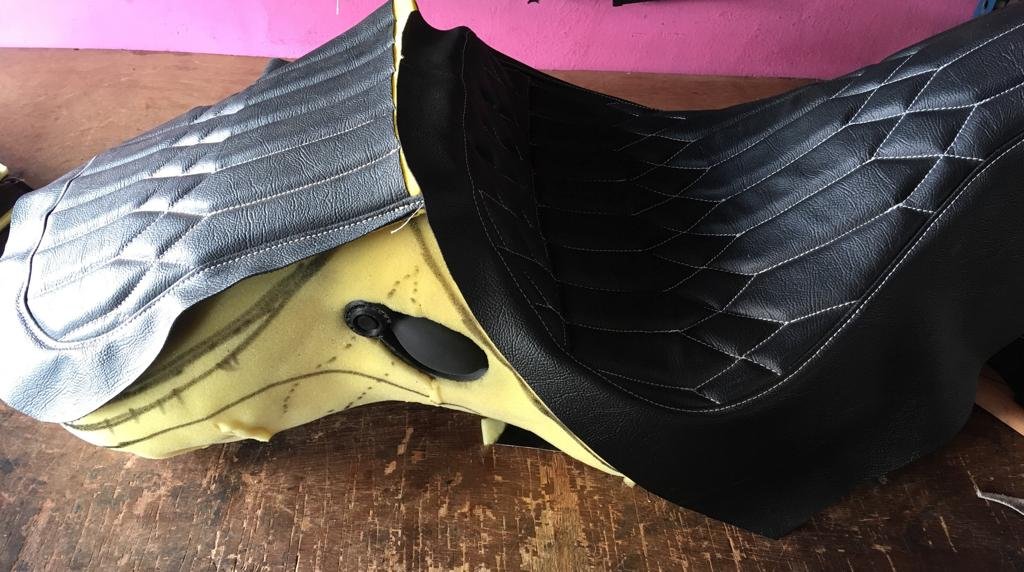
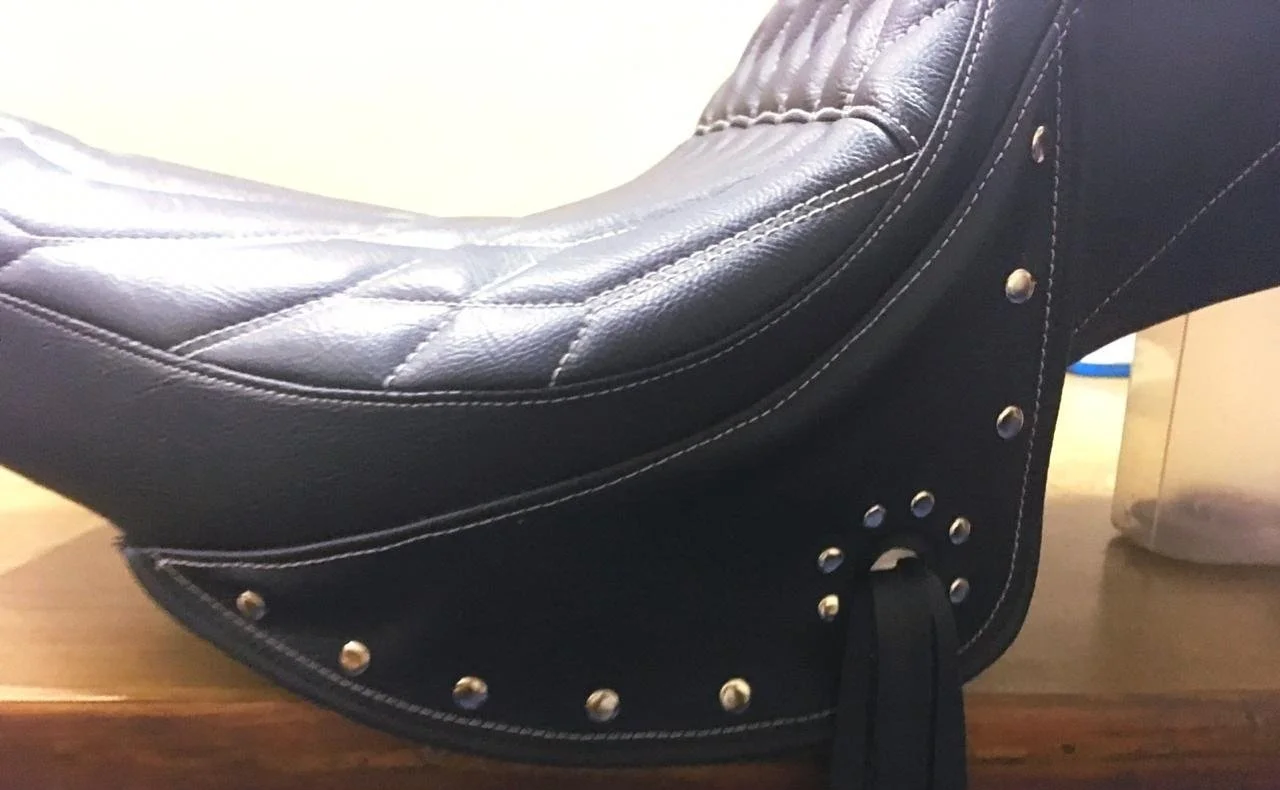
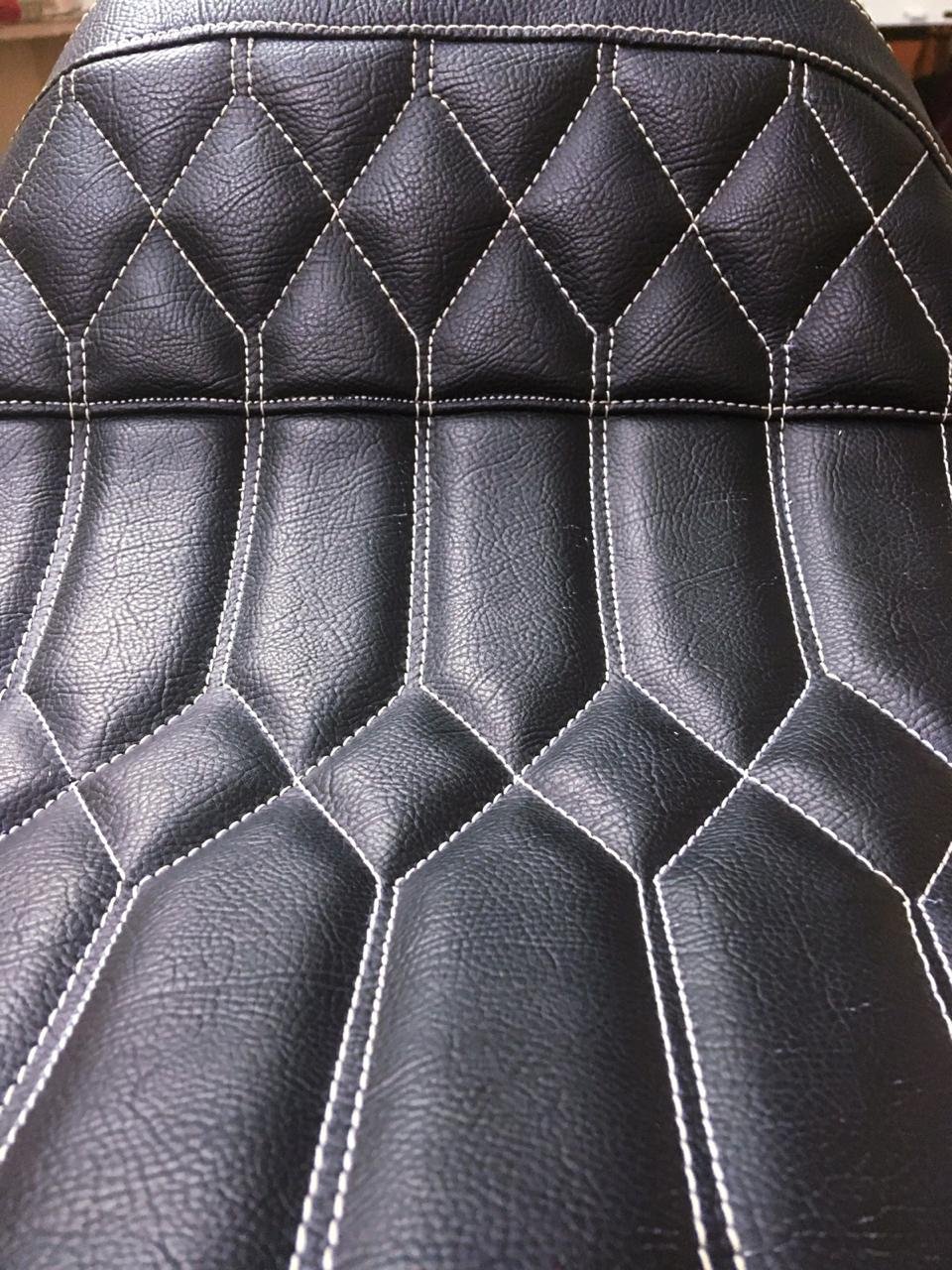
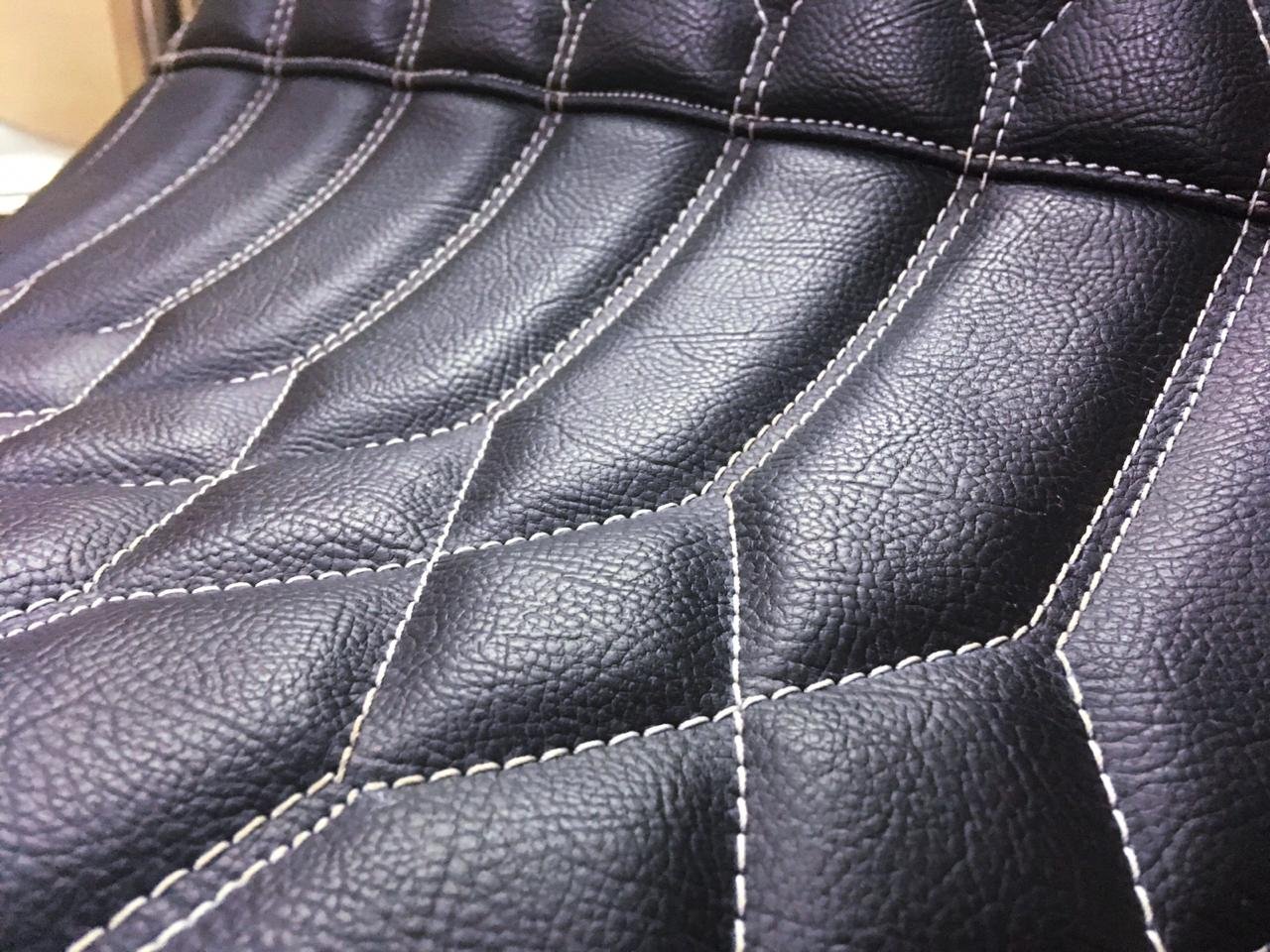
RESULTS
Improved ride time/saddle time for the user by 2X
Delighted with the comfort and praise received from fellow riders for the looks, the user signed me up for two more projects.
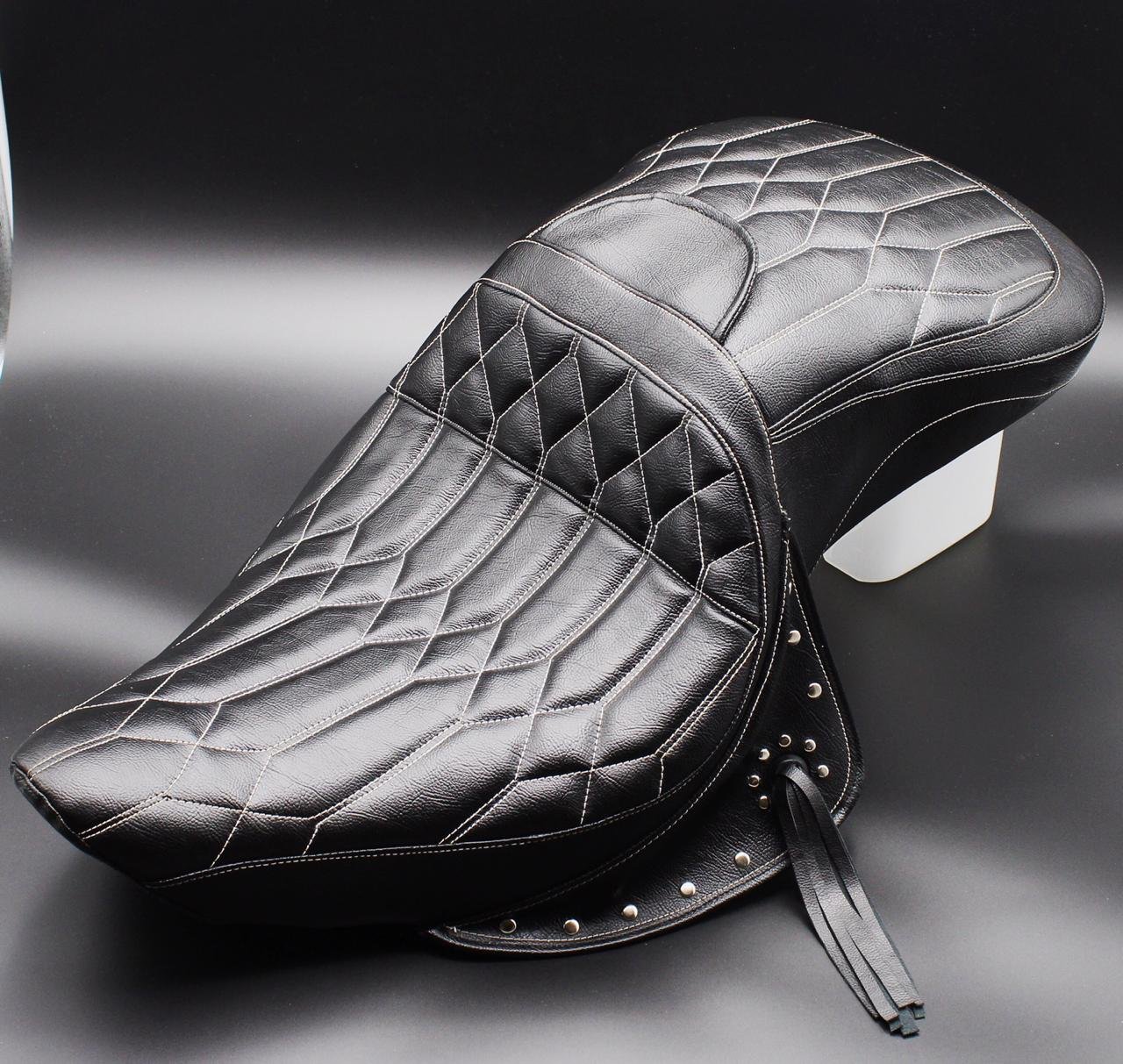
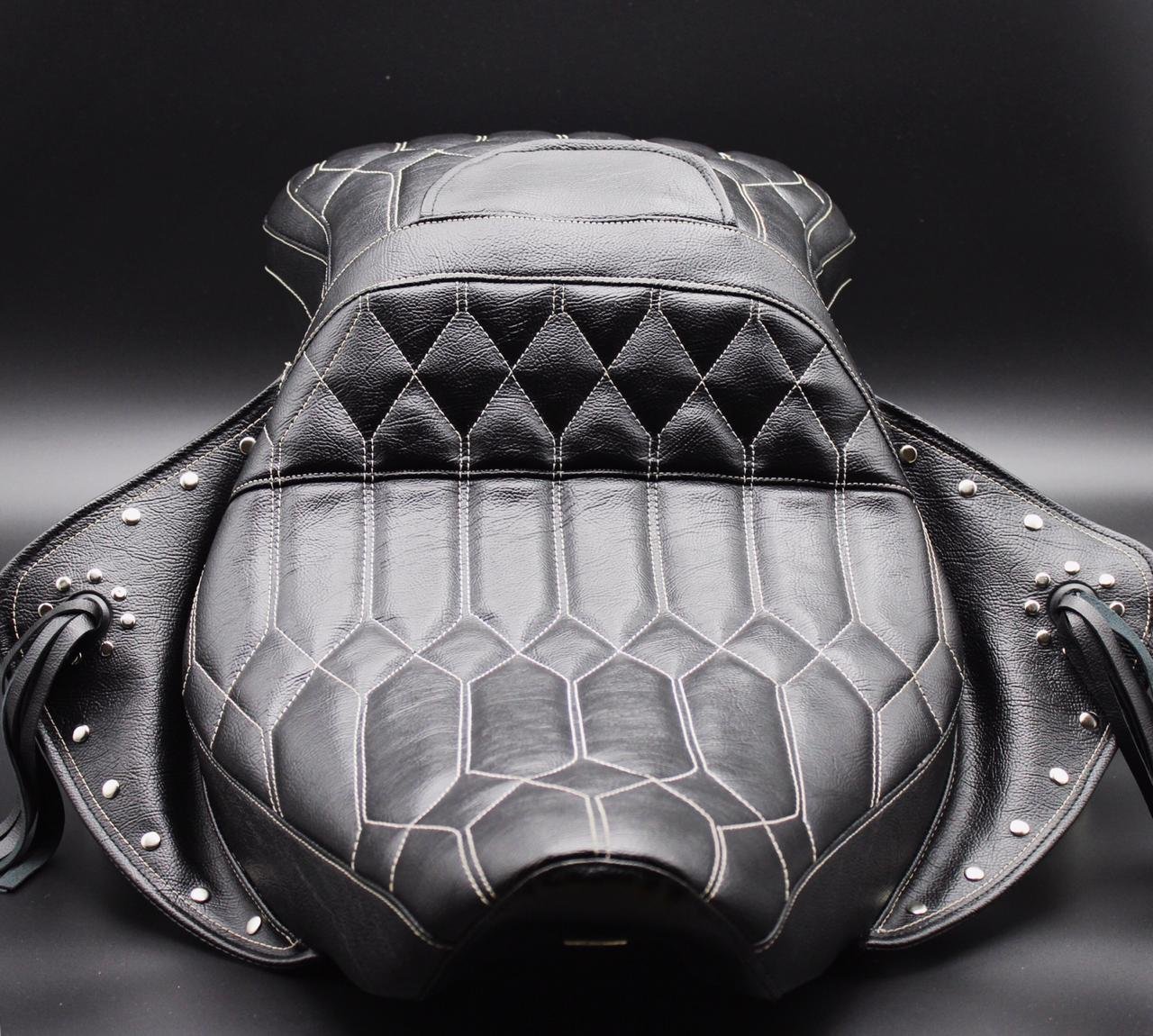
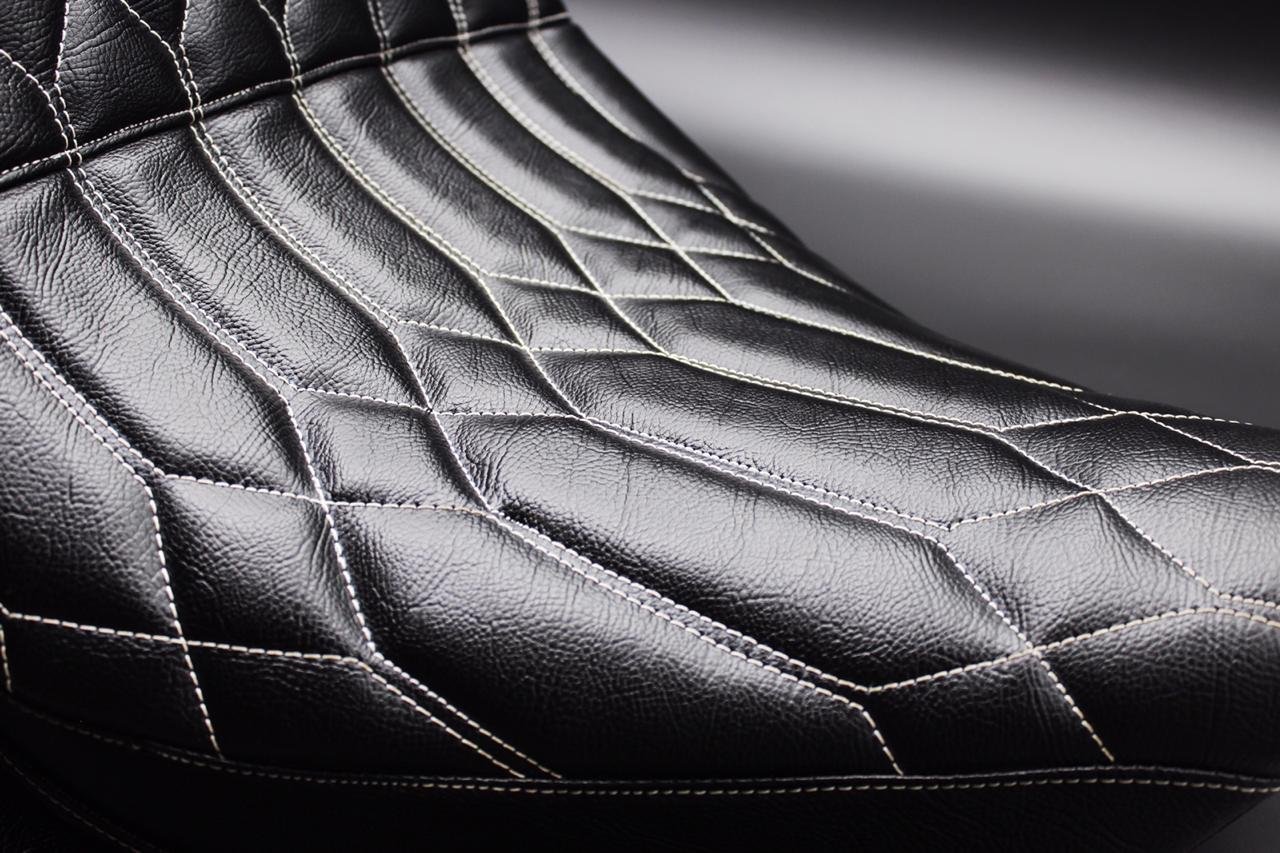



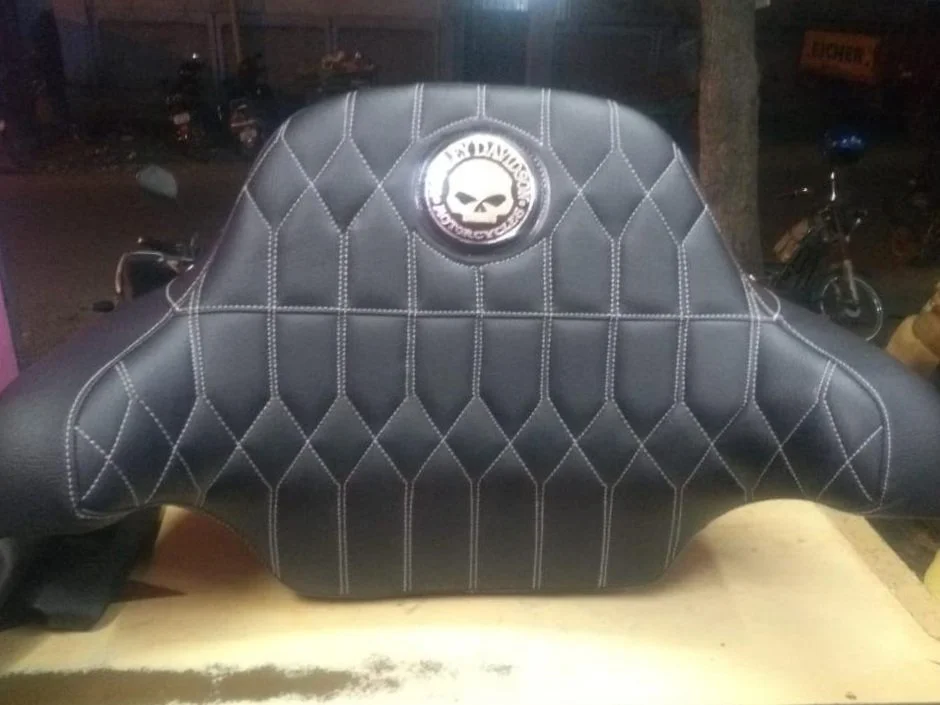
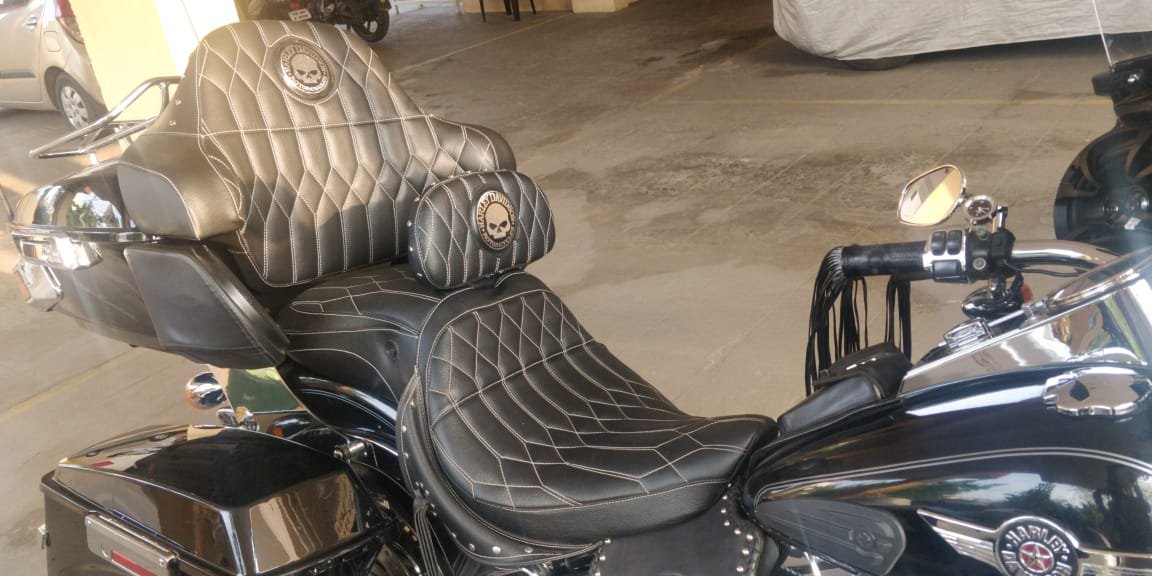
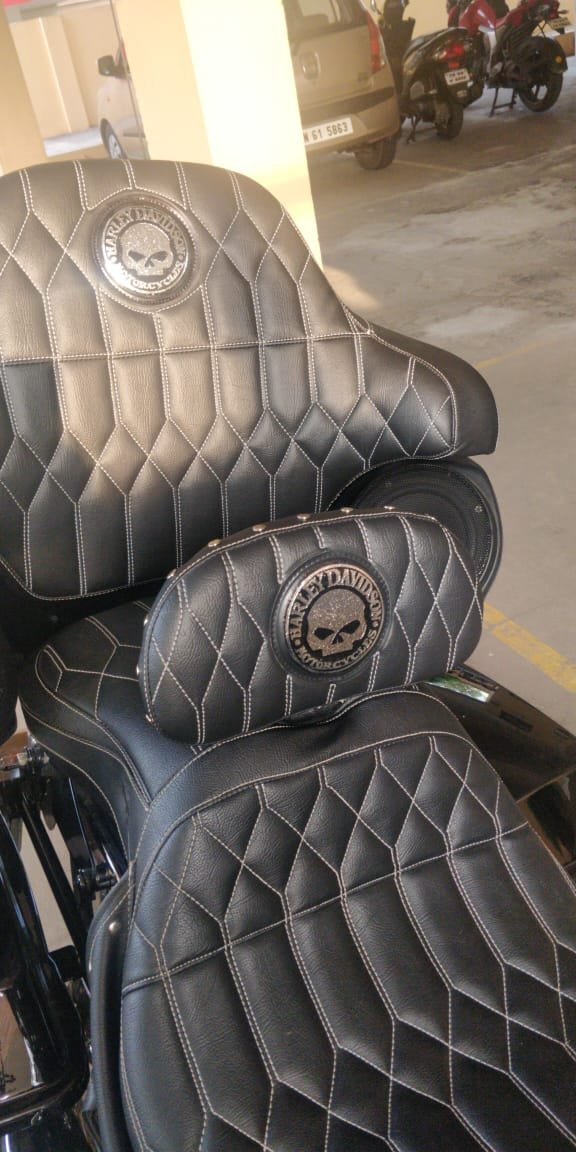